Organosilicon release agent with ultra-light release force and preparation method thereof
A technology of ultra-light release and release agent, which is applied in the direction of film/sheet adhesives, adhesives, coatings, etc., and can solve problems such as complex process, reduced release force, and abnormal product release force. Broaden the application field, reduce the release force, and facilitate procurement
- Summary
- Abstract
- Description
- Claims
- Application Information
AI Technical Summary
Problems solved by technology
Method used
Examples
Embodiment 1
[0047] 100 parts of vinyl-terminated polydimethylsiloxane (viscosity 150mPa s, vinyl mass fraction 0.80%), 2.8 parts of methyl hydrogen-containing silicone oil (100mPa s, hydrogen content 1.6%), Add 0.7 parts of amino silicone oil (viscosity of 350 mPa s, ammonia value of 0.4), 0.3 parts of methyl fluorosilicone oil (viscosity of 550 mPa s, molar ratio of trifluoropropyl group 10%) into the container, control Stirring speed is 300-500 rpm, closed stirring for 5 minutes; then add 0.5 parts of spherical silicon micropowder, 0.3 parts of white carbon black, 1800 rpm high-speed shear stirring for 2 hours, then continue to add 1 part of anchoring agent, 0.1 part of inhibitor , 300 parts of toluene, control the stirring speed to 300-500 rpm, closed stirring for 5 minutes; finally add 3 parts of platinum catalyst, closed stirring for 5 minutes to obtain a silicone release agent with ultra-light release force.
Embodiment 2
[0049] 100 parts of vinyl-terminated polydimethylsiloxane (viscosity 150mPa s, vinyl mass fraction 0.80%), 2.8 parts of methyl hydrogen-containing silicone oil (100mPa s, hydrogen content 1.6%), Add 0.5 parts of amino silicone oil (viscosity of 350 mPa•s, ammonia value of 0.4), 0.5 parts of methyl fluorosilicone oil (viscosity of 550 mPa•s, molar ratio of trifluoropropyl group to 10%) into the container, control Stirring speed is 300-500 rpm, closed stirring for 5 minutes; then add 0.5 parts of spherical silicon micropowder, 0.3 parts of white carbon black, 1800 rpm high-speed shear stirring for 2 hours, then continue to add 1 part of anchoring agent, 0.1 part of inhibitor , 300 parts of 120# solvent oil, control the stirring speed to 300-500 rpm, closed and stirred for 5 minutes; finally add 3 parts of platinum catalyst, closed and stirred for 5 minutes to obtain a silicone release agent with ultra-light release force.
Embodiment 3
[0051] 100 parts of vinyl-terminated polydimethylsiloxane (viscosity 150mPa s, vinyl mass fraction 0.80%), 2.8 parts of methyl hydrogen-containing silicone oil (100mPa s, hydrogen content 1.6%), 0.3 parts of amino silicone oil (viscosity of 350 mPa s, ammonia value 0.4), 0.7 parts of methyl fluorosilicone oil (viscosity of 550 mPa s, molar ratio of trifluoropropyl group 10%) were added to the container, and the control Stirring speed is 300-500 rpm, closed stirring for 5 minutes; then add 0.5 parts of spherical silicon micropowder, 0.3 parts of white carbon black, 1800 rpm high-speed shear stirring for 2 hours, then continue to add 1 part of anchoring agent, 0.1 part of inhibitor 1. 300 parts of xylene, control the stirring speed to 300-500 rpm, closed stirring for 5 minutes; finally add 3 parts of platinum catalyst, closed stirring for 5 minutes to obtain a silicone release agent with ultra-light release force.
PUM
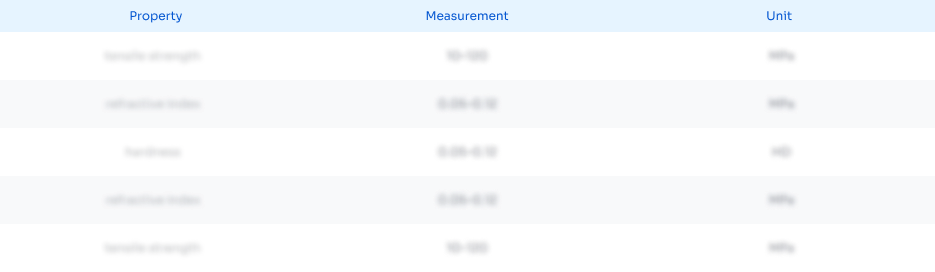
Abstract
Description
Claims
Application Information

- R&D Engineer
- R&D Manager
- IP Professional
- Industry Leading Data Capabilities
- Powerful AI technology
- Patent DNA Extraction
Browse by: Latest US Patents, China's latest patents, Technical Efficacy Thesaurus, Application Domain, Technology Topic, Popular Technical Reports.
© 2024 PatSnap. All rights reserved.Legal|Privacy policy|Modern Slavery Act Transparency Statement|Sitemap|About US| Contact US: help@patsnap.com