Production method of composite metal oxide functional electrode
A composite metal and oxide technology, applied in chemical instruments and methods, water pollutants, water/sewage treatment, etc., can solve the problems of precious metal loss, complicated preparation steps, limited loading of cobalt tetroxide, etc., and achieve low concentration of intermediate by-products , The engineering application prospect is broad, and the effect of reduction and removal can be realized efficiently
- Summary
- Abstract
- Description
- Claims
- Application Information
AI Technical Summary
Problems solved by technology
Method used
Image
Examples
Embodiment 1
[0033] This embodiment provides a method for preparing a composite metal oxide functional electrode, which includes:
[0034] (1) Carbon cloth base pretreatment:
[0035] First, cut out a carbon cloth with a size of 2×2 cm, and then perform ultrasonic cleaning on it with acetone and absolute ethanol to remove surface stains. The ultrasonic cleaning time is 30 minutes, and the power is 90W; the cleaned carbon cloth is rinsed with deionized water 3 times to remove residual acetone and absolute ethanol on the surface; then soak the carbon cloth in 3mol / L nitric acid solution for 12 hours to remove impurities such as inorganic oxides on the surface of the carbon cloth, and then rinse it with deionized water; finally, the carbon cloth Arranged in a vacuum drying oven, vacuum-dry at 60°C for 12 hours, and the vacuum degree is -0.1MPa;
[0036] (2) Co(OH) used in the preparation of functional electrodes 2 / Cu(OH) 2 Precursor preparation:
[0037] ①Chemical raw materials used:
...
Embodiment 2
[0058] This embodiment provides a method for preparing a composite metal oxide functional electrode, which includes:
[0059] (1) Carbon cloth base pretreatment:
[0060] First, cut out a carbon cloth with a size of 2×2 cm, and then perform ultrasonic cleaning on it with acetone and absolute ethanol to remove surface stains. The ultrasonic cleaning time is 40 minutes, and the power is 90W; the cleaned carbon cloth is rinsed with deionized water 3 times to remove residual acetone and absolute ethanol on the surface; then soak the carbon cloth in 3mol / L nitric acid solution for 12 hours to remove impurities such as inorganic oxides on the surface of the carbon cloth, and then rinse it with deionized water; finally, the carbon cloth Arranged in a vacuum drying oven, vacuum-dry at 65°C for 12 hours, and the vacuum degree is -0.1MPa;
[0061] (2) Co(OH) used in the preparation of functional electrodes 2 / Cu(OH) 2 Precursor preparation:
[0062] ①Chemical raw materials used:
...
experiment example
[0075] Experimental procedure is basically consistent with embodiment 1, and difference is:
[0076] (1) The concentration of nitrate nitrogen in the electrolyte solution is 50mg / L, the concentration of sodium sulfate is 0.1g / L, and the concentration of sodium chloride is 2g / L.
[0077] (2) When using the constant current mode to reduce the nitrate in the solution, the cathode current is controlled at 0.08A, and the reduction treatment time is 180min.
[0078] Experimental results: Figure 5 Be CoO / Cu in embodiment 2 2 O functional electrode, Cu 2 Nitrate removal rate and product concentration diagram of O electrode and CoO electrode, CoO / Cu 2 The removal rate of nitrate by O functional electrode is 91.4%, and its performance on nitrate removal is better than that of CoO electrode, Cu 2 O electrode, during the reaction process, the concentration of intermediate products nitrite and ammonium salt first increases and then decreases, and finally decreases to 0.
PUM
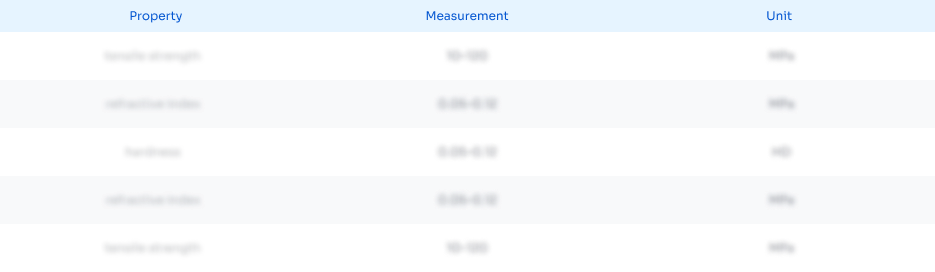
Abstract
Description
Claims
Application Information

- Generate Ideas
- Intellectual Property
- Life Sciences
- Materials
- Tech Scout
- Unparalleled Data Quality
- Higher Quality Content
- 60% Fewer Hallucinations
Browse by: Latest US Patents, China's latest patents, Technical Efficacy Thesaurus, Application Domain, Technology Topic, Popular Technical Reports.
© 2025 PatSnap. All rights reserved.Legal|Privacy policy|Modern Slavery Act Transparency Statement|Sitemap|About US| Contact US: help@patsnap.com