Linear quadratic type optimal dynamic feedforward-feedback PID control system based on closed-loop identification model and control method thereof
A linear quadratic, dynamic feedforward technology, applied in general control systems, control/regulation systems, adaptive control, etc., can solve problems such as difficulty in using non-minimum phase systems, limited performance of static feedforward controllers, etc.
- Summary
- Abstract
- Description
- Claims
- Application Information
AI Technical Summary
Problems solved by technology
Method used
Image
Examples
Embodiment Construction
[0098] The technical solution of the present invention will be described in detail below in conjunction with the accompanying drawings and specific embodiments.
[0099]The present invention proposes a novel dynamic feedforward-feedback control scheme for non-minimum phase control systems of thermal power units, wherein the feedforward controller is a discrete state space form based on a linear quadratic regulator (LQR) design The optimal linear quadratic dynamic feedforward controller avoids the influence of the right half plane zero point of the disturbance model in the design of conventional dynamic feedforward for non-minimum phase systems.
[0100] The thermal power unit includes various control loops. The present invention takes the actual data of the deaerator water level control system of a power plant in Nanjing as an example to simulate, and further elaborates on the technical solution of the present invention:
[0101] Such as figure 1 As shown, the optimal quadrat...
PUM
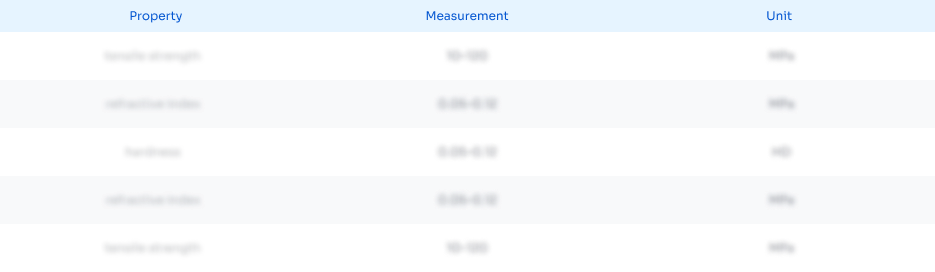
Abstract
Description
Claims
Application Information

- Generate Ideas
- Intellectual Property
- Life Sciences
- Materials
- Tech Scout
- Unparalleled Data Quality
- Higher Quality Content
- 60% Fewer Hallucinations
Browse by: Latest US Patents, China's latest patents, Technical Efficacy Thesaurus, Application Domain, Technology Topic, Popular Technical Reports.
© 2025 PatSnap. All rights reserved.Legal|Privacy policy|Modern Slavery Act Transparency Statement|Sitemap|About US| Contact US: help@patsnap.com