Automatic packaging tape winding system
An adhesive tape and automatic technology, applied in the direction of packaging/bundling items, packaging, wrapping items, etc., can solve the problems of dust and oil on the surface of the workpiece, poor quality of packaging products, and low degree of automation, saving manpower and material resources and reducing the weight of the body. , the effect of high degree of automation
- Summary
- Abstract
- Description
- Claims
- Application Information
AI Technical Summary
Problems solved by technology
Method used
Image
Examples
Embodiment 1
[0036] Such as Figure 1-7 As shown, an automatic tape winding system described in this embodiment includes a frame 1, a rotating tape sticking device 2, a tape smoothing and cutting device 3, a workpiece supporting device 4, a tape pressing device 5 and a workpiece pressing device 6.
[0037] The rotary taping device is installed on the front end of the frame, including a drive assembly, a slewing support 21 rotatably connected to the frame, and a tape applicator connected to the slewing support; the drive assembly is connected to the slewing support, and the drive assembly drives the slewing support to rotate. There is a through hole in the middle of the slewing support, and there is a gap corresponding to the position of the through hole on the frame for placing the workpiece.
[0038] The drive assembly includes a servo motor 27 and a transmission gear 22. The slewing support is circular, and the outer surface of the slewing support has transmission teeth that match the t...
Embodiment 2
[0055] The difference between this embodiment and Embodiment 1 is that there is a baffle 24 at the end of the adhesive tape fixing sleeve near the slewing support, and a detection hole 241 is provided on the baffle, and the detection holes are arranged in a ring on the baffle, and the baffle can limit the tape The fixed position of the roll, with a detection device on the frame, the detection signal of the detection device passes through the detection hole to detect the remaining thickness of the tape roll, which is convenient for timely replacement of the tape roll; the detection device corresponds to the initial position of the tape fixed sleeve, and the detection process is The prior art will not be described in detail here.
Embodiment 3
[0057] The difference between this embodiment and Embodiment 1 and Embodiment 2 is that the adhesive tape fixing sleeve is provided with a movable groove 231, a movable block 232 is installed on the movable groove, a spring is installed between the movable block and the movable groove, and the movable block moves towards the movable groove. Internal activities, the tape roll is covered on the tape fixing sleeve, and then under the action of the spring restoring force, the movable block resets, and the tape roll is clamped on the tape fixing sleeve to prevent the tape roll from sliding.
PUM
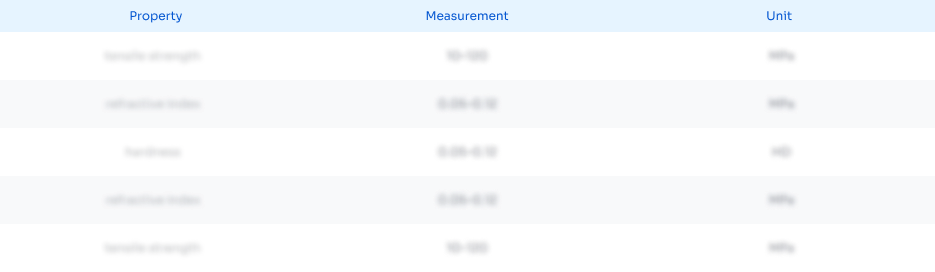
Abstract
Description
Claims
Application Information

- R&D
- Intellectual Property
- Life Sciences
- Materials
- Tech Scout
- Unparalleled Data Quality
- Higher Quality Content
- 60% Fewer Hallucinations
Browse by: Latest US Patents, China's latest patents, Technical Efficacy Thesaurus, Application Domain, Technology Topic, Popular Technical Reports.
© 2025 PatSnap. All rights reserved.Legal|Privacy policy|Modern Slavery Act Transparency Statement|Sitemap|About US| Contact US: help@patsnap.com