A method for pyro-reduction smelting bismuth to enrich platinum group metals in waste automobile exhaust catalysts
An auto catalyst and platinum group metal technology, applied in the direction of improving process efficiency, can solve the problems of not being well suited for platinum group metal enrichment treatment and high smelting temperature, so as to reduce the difficulty of separation and recovery, eliminate low recovery rate, Good enrichment effect
- Summary
- Abstract
- Description
- Claims
- Application Information
AI Technical Summary
Problems solved by technology
Method used
Image
Examples
Embodiment 1
[0053] Step 1. Ingredients
[0054] A waste automobile exhaust catalyst was coarsely crushed and finely crushed, and the particle size was 200 meshes. Accurately weighed 50.00g and put it into a clay crucible, added 3.71g of bismuth oxide, 4.16g of bismuth oxychloride and 4.16g of bismuth hydroxide, and then added sodium carbonate 35.00g, 31.09g of sodium bicarbonate, 28.78g of sodium hydroxide and 32.14g of potassium carbonate, then add 0.21g of wheat flour, 0.10g of coke powder and 0.10g of sweet potato powder, stir well, the silicic acidity of the material is K=0.5, and finally add The covering agent 4.5g that is made up of sodium carbonate and silicon dioxide by the mass ratio of 100:14 fully covers batching (the silicic acid degree of this embodiment is lower, and the silicon dioxide contained in the waste and old automobile exhaust catalyst can satisfy the requirement of batching. Silicic acidity requirements, so there is no need to add acidic silicon or silicon dioxide ...
Embodiment 2
[0060] Step 1. Ingredients
[0061] A waste automobile exhaust catalyst was coarsely crushed and finely crushed to a particle size of 200 mesh, and 50.00 g was accurately weighed and put into a clay crucible, and 13.30 g of sodium bismuthate, 14.07 g of potassium bismuthate, 5.57 g of bismuth oxide and 6.25 g of bismuth oxychloride were added respectively. g, then add 50.00g of sodium carbonate, 40.10g of borax, 58.82g of boric acid and 15.01g of silicon dioxide, then add 0.50g of wheat flour, 0.21g of coke powder and 0.21g of coal powder, stir well, and the silicic acidity of the material K=1.3 , and finally add 12.5g of covering agent composed of sodium carbonate, potassium carbonate and silicon dioxide in a mass ratio of 50:50:30 to fully cover the ingredients.
[0062] Step 2. Primary smelting and capture
[0063] Put the above prepared crucible into a muffle furnace that has been heated to 800°C, and raise the temperature to 1100°C in 60 minutes. Stir properly during the...
Embodiment 3
[0067] Step 1. Ingredients
[0068] A waste automobile exhaust catalyst was coarsely crushed and finely crushed to a particle size of 200 meshes, and 50.00 g was accurately weighed and put into a clay crucible, and 13.30 g of sodium bismuthate, 14.07 g of potassium bismuthate, 11.15 g of bismuth oxide, and 12.50 g of bismuth oxychloride g and bismuth hydroxide 12.50g, then add sodium carbonate 20.00g, potassium carbonate 20.00g, sodium formate 10.00g, sodium acetate 10.01g, sodium bicarbonate 10.01g, calcium oxide 5.00g, borax 60.00g, boric acid 38.82g and dioxide Silicon 45.50g, then add wheat flour 1.00g, coke powder 0.21g and sweet potato flour 1.00g, fully stir, the material silicic acidity K=2.2, finally add sodium carbonate, potassium carbonate, borax, silicon dioxide according to 33: 15g of covering agent composed of 17:30:20 mass ratio will cover the ingredients evenly.
[0069] Step 2. Primary smelting and capture
[0070] Put the above prepared crucible into a muff...
PUM
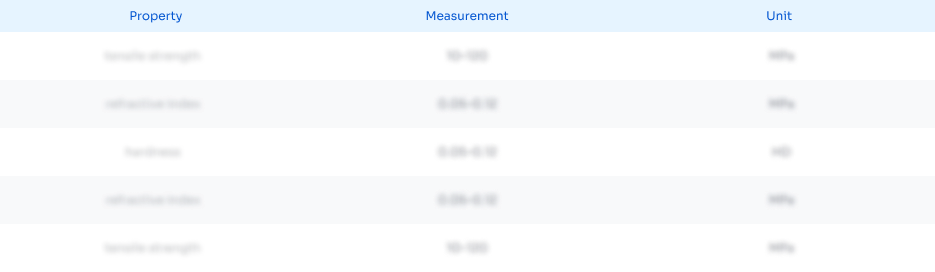
Abstract
Description
Claims
Application Information

- Generate Ideas
- Intellectual Property
- Life Sciences
- Materials
- Tech Scout
- Unparalleled Data Quality
- Higher Quality Content
- 60% Fewer Hallucinations
Browse by: Latest US Patents, China's latest patents, Technical Efficacy Thesaurus, Application Domain, Technology Topic, Popular Technical Reports.
© 2025 PatSnap. All rights reserved.Legal|Privacy policy|Modern Slavery Act Transparency Statement|Sitemap|About US| Contact US: help@patsnap.com