Equipment for automatically separating plywood veneers and screening and gluing single veneers
A technology for automatic separation and plywood, which is applied to the device, sorting, coating and other directions of coating liquid on the surface, which can solve the problems of affecting the quality of the veneer, unable to ensure stable output, and excessive glue impurities in the glue tank of the glue coating machine. , to reduce labor intensity and labor risks, solve the problem of repeated positioning accuracy, and facilitate daily maintenance and maintenance.
- Summary
- Abstract
- Description
- Claims
- Application Information
AI Technical Summary
Problems solved by technology
Method used
Image
Examples
Embodiment Construction
[0019] Below in conjunction with accompanying drawing, preferred embodiment of the present invention is further described:
[0020] Such as figure 1 As shown, a plywood veneer is automatically separated and screened out single sheets and glued. The material preparation mechanism 1 is connected and fixed at one end of the conveying mechanism 2, and the other end of the conveying mechanism 2 is fixedly connected with the sorting mechanism 3. The conveying mechanism 2 is correspondingly provided with a conveying platform, and the rear end of the conveying platform is provided with a scraper assembly 21, and the scraper assembly 21 is fixed on the conveying frame by screws, and the sorting mechanism 3 is equipped with a number detection device. System 31 and impurity removal device 32, the gluing mechanism 4 is fixed on the sorting mechanism 3 through connection, the automatic gluing system 41 is installed on the upper part of the gluing mechanism 4, and the receiving mechanism 5 ...
PUM
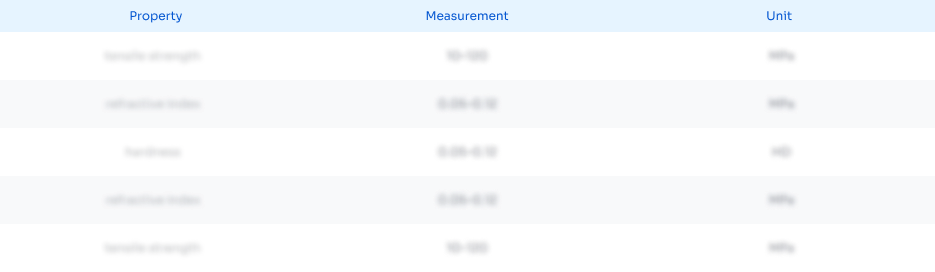
Abstract
Description
Claims
Application Information

- R&D
- Intellectual Property
- Life Sciences
- Materials
- Tech Scout
- Unparalleled Data Quality
- Higher Quality Content
- 60% Fewer Hallucinations
Browse by: Latest US Patents, China's latest patents, Technical Efficacy Thesaurus, Application Domain, Technology Topic, Popular Technical Reports.
© 2025 PatSnap. All rights reserved.Legal|Privacy policy|Modern Slavery Act Transparency Statement|Sitemap|About US| Contact US: help@patsnap.com