Laser microstructure machining machine tool repeated positioning control method and machine tool control system
A technology for machining machine tools and repetitive positioning, which is applied to machine tool control systems and the field of repetitive positioning control of laser microtexturing machine tools. , Improve the focus dislocation problem, and the effect of improving the repeatability of the system
- Summary
- Abstract
- Description
- Claims
- Application Information
AI Technical Summary
Problems solved by technology
Method used
Image
Examples
Embodiment Construction
[0050] The present invention will be further described in detail below in conjunction with the accompanying drawings.
[0051] like figure 1 A method for controlling repetitive positioning of a laser microtexturing machine tool is shown, including the following steps:
[0052] Step 1. Obtain the configuration information of the machine tool workbench, the configuration information includes the motion trajectory, speed and acceleration of the machine tool workbench;
[0053] Step 2, establishing a mathematical model of the transmission link of the machine tool, and calculating the ideal values of the rotational speed and acceleration of each servo motor in combination with the configuration information;
[0054] Step 3. Read the actual values of the speed and acceleration of each servo motor and compare them with the ideal values to obtain the setting parameters of the composite feedforward compensation of speed and acceleration, and obtain the feedforward compensation v...
PUM
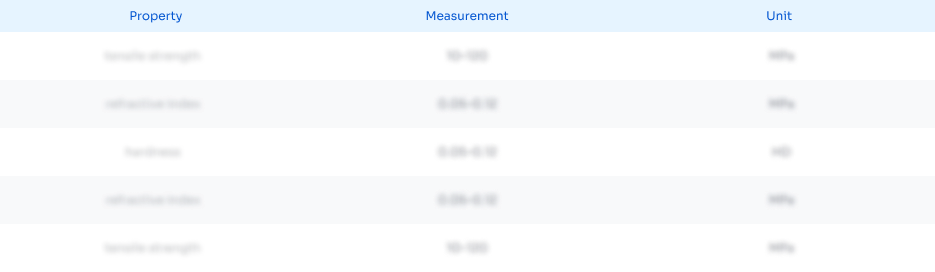
Abstract
Description
Claims
Application Information

- R&D
- Intellectual Property
- Life Sciences
- Materials
- Tech Scout
- Unparalleled Data Quality
- Higher Quality Content
- 60% Fewer Hallucinations
Browse by: Latest US Patents, China's latest patents, Technical Efficacy Thesaurus, Application Domain, Technology Topic, Popular Technical Reports.
© 2025 PatSnap. All rights reserved.Legal|Privacy policy|Modern Slavery Act Transparency Statement|Sitemap|About US| Contact US: help@patsnap.com