Connecting structure of prefabricated column and superposed beam as well as construction method of connecting structure
A technology for connecting structures and prefabricated columns, which is applied in the direction of building construction and construction, can solve the problems of inconvenient construction and low tolerance, and achieve the effects of easy and adjustable installation, complete force transmission path, and reduced number of supporting forms
- Summary
- Abstract
- Description
- Claims
- Application Information
AI Technical Summary
Problems solved by technology
Method used
Image
Examples
Embodiment 1
[0053] Reference attached figure 1 As shown, this embodiment is a connection structure between a prefabricated column 1 and a composite beam 2 , and the composite beam 2 includes a prefabricated part 201 and a cast-in-place part 202 . The height of the prefabricated column 1 exceeds the height of one floor. In this embodiment, it is a prefabricated column 1 with a height of 3 floors. In other embodiments, prefabricated columns 1 with a height of 1-2 floors can also be used. Prefabricated columns 1 in height between 3 storeys. The end of the composite beam 2 is connected to the side of the precast column 1, the precast column 1 is connected to the lower longitudinal reinforcement 6 in the cast-in-place part 202 through the longitudinal reinforcement connection assembly 14, and the upper longitudinal reinforcement 5 in the cast-in-place part 202 is connected to the precast column 1 For connection, the distance between the upper longitudinal rib 5 and the top surface of the pref...
Embodiment 2
[0070] This embodiment is the connection structure between the prefabricated column 1 and two composite beams 2, refer to the attached Figure 5 As shown, when the composite beams 2 are arranged on both sides of the prefabricated column 1, the connection structure on each side is roughly the same as that in Embodiment 1. The difference is that both ends of the upper transverse anchoring rib 7 in the prefabricated column 1 are provided with first sleeves 10, both ends of the lower transverse anchoring rib 8 are provided with second sleeves 10, and the first sleeve 10 and the second sleeve 10 are both anchored in the concrete of the prefabricated column 1 , and the end surface of the sleeve 10 is slightly lower than or flush with the side surface of the precast column 1 .
[0071] In the improved solution of this embodiment, the upper transverse anchor bars 7 and the lower transverse anchor bars 8 can be provided with anchor plates or anchor legs or anchor nets to enhance the an...
Embodiment 3
[0074] Reference attached Image 6 As shown, the difference between the connection structure of prefabricated columns 1 and composite beams 2 in this embodiment and this embodiment 1 is that a prefabricated exterior wall panel 3 is also provided on the outdoor side of the column-beam structure in embodiment 5. The prefabricated exterior wall panel 3 is fixed to the composite beam 2 through connectors, and the height of the top side of the prefabricated exterior wall panel 3 is slightly higher than or flush with the top side of the cast-in-place part 202 of the composite beam 2, so the height of the poured composite beam 2 When the concrete of the part 202 is poured in place, the top side of the prefabricated exterior wall panel 3 can serve as an outer formwork, which reduces the workload of formwork erection and improves construction efficiency.
[0075] The difference between the construction method in this embodiment and Embodiment 1 is that: between steps S4 and S5, there i...
PUM
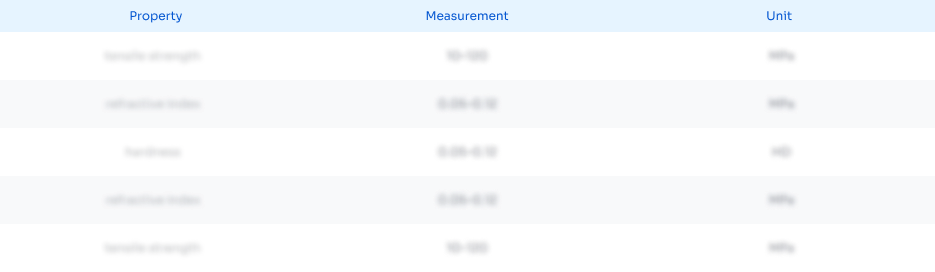
Abstract
Description
Claims
Application Information

- R&D Engineer
- R&D Manager
- IP Professional
- Industry Leading Data Capabilities
- Powerful AI technology
- Patent DNA Extraction
Browse by: Latest US Patents, China's latest patents, Technical Efficacy Thesaurus, Application Domain, Technology Topic, Popular Technical Reports.
© 2024 PatSnap. All rights reserved.Legal|Privacy policy|Modern Slavery Act Transparency Statement|Sitemap|About US| Contact US: help@patsnap.com