Multi-station induction heating circuit and heating and control method thereof
An induction heating, multi-station technology, applied in induction heating control, induction heating and other directions, can solve the problem that the control circuit cannot accurately capture and determine the heating situation of the heating coil, the workpiece cannot obtain the ideal heating effect, and the magnetic field signal is disordered. Good heating effect, high reliability of the circuit as a whole, and the effect of reducing processing costs
- Summary
- Abstract
- Description
- Claims
- Application Information
AI Technical Summary
Problems solved by technology
Method used
Image
Examples
Embodiment Construction
[0037] In order to make the object, technical solution and advantages of the present invention clearer, the present invention will be further described in detail below in conjunction with the accompanying drawings and embodiments. It should be understood that the specific embodiments described here are only used to explain the present invention, not to limit the present invention.
[0038] To achieve the above object, the technical scheme of the present invention is as follows:
[0039] see figure 1 As shown, the present invention provides a multi-station induction heating circuit, the circuit includes a power converter, the power converter includes a rectification module M1, a voltage regulation module M2 and an inverter module M3, a rectification module M1, a voltage regulation module M2 It is connected with the inverter module M3 in sequence, and the input end of the rectification module M1 is connected with an external three-phase network voltage; the output end of the in...
PUM
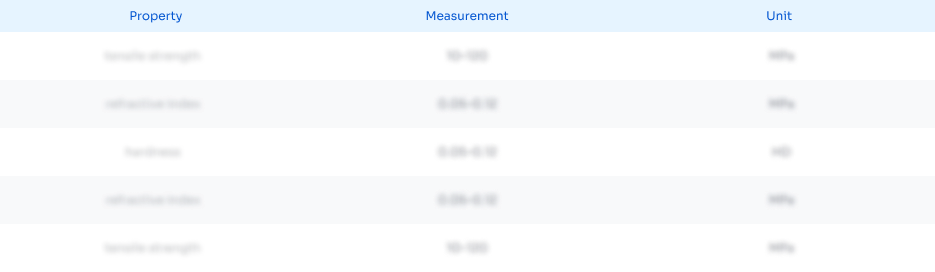
Abstract
Description
Claims
Application Information

- R&D Engineer
- R&D Manager
- IP Professional
- Industry Leading Data Capabilities
- Powerful AI technology
- Patent DNA Extraction
Browse by: Latest US Patents, China's latest patents, Technical Efficacy Thesaurus, Application Domain, Technology Topic, Popular Technical Reports.
© 2024 PatSnap. All rights reserved.Legal|Privacy policy|Modern Slavery Act Transparency Statement|Sitemap|About US| Contact US: help@patsnap.com