Sodium silicate-bonded sand for casting and hardening method thereof
A technology of water glass sand and water glass, which is applied in the direction of casting molding equipment, casting molds, manufacturing tools, etc., can solve the problems of hindering reaction, easy moisture absorption of sand mold, moisture absorption of water glass sand, etc., so as to improve the casting yield and improve Sand mold collapsibility and the effect of reducing old sand discharge
- Summary
- Abstract
- Description
- Claims
- Application Information
AI Technical Summary
Problems solved by technology
Method used
Examples
Embodiment 1
[0038] In terms of parts by mass, take 10,000 parts of scrubbing sand, 300 parts of water glass, 48 parts of hardening accelerator (a mixture of ferrous sulfate and glycerin, ratio 1:1), and 15 parts of modifier (sodium pyrophosphate) and mix evenly. Prepare water glass sand 1.
[0039] Make "8" shape sand sample with above-mentioned water glass sand 1, blow into CO 2 , until the tensile strength reaches 0.16MPa, demould, and let stand.
[0040] The 24h tensile strength of the sample obtained in Example 1 can reach 0.46MPa, the 72h wet strength is 0.43MPa, and the residual strength at 800°C is 0.11MPa, which has good strength, good moisture resistance and high collapsibility.
Embodiment 2
[0042] In terms of parts by mass, take 10,000 parts of scrubbing sand, 300 parts of water glass, 48 parts of hardener (a mixture of ferrous sulfate and glycerin, ratio 1:1), ester (a mixture of glyceryl acetate and glyceryl triacetate, Mix 50 parts (ratio 1:1) and 15 parts water-repellent agent (sodium methyl siliconate) evenly to prepare water glass sand 2.
[0043] Make 8-shaped sand sample with above-mentioned water glass sand 2, blow into CO 2 , until its tensile strength reaches 0.16MPa, demould, and stand still.
[0044] The 24h tensile strength of the sample obtained in Example 2 can reach 0.48MPa, the 72h wet strength is 0.47MPa, and the residual strength at 800°C is 0.09MPa, which has good strength, good moisture resistance, and high collapsibility.
PUM
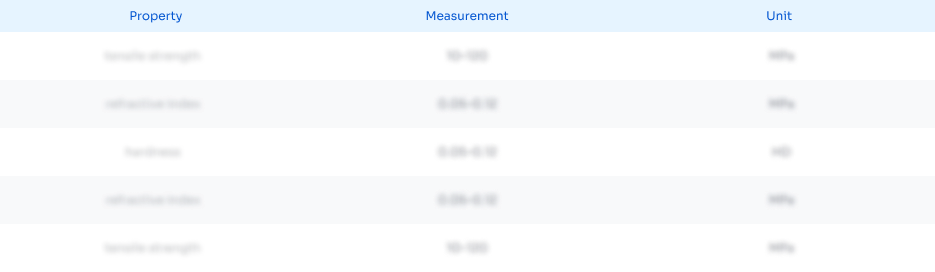
Abstract
Description
Claims
Application Information

- Generate Ideas
- Intellectual Property
- Life Sciences
- Materials
- Tech Scout
- Unparalleled Data Quality
- Higher Quality Content
- 60% Fewer Hallucinations
Browse by: Latest US Patents, China's latest patents, Technical Efficacy Thesaurus, Application Domain, Technology Topic, Popular Technical Reports.
© 2025 PatSnap. All rights reserved.Legal|Privacy policy|Modern Slavery Act Transparency Statement|Sitemap|About US| Contact US: help@patsnap.com