Highly-stable composite die base material
A composite mold, stable technology, applied in the field of composite mold base materials, can solve the problems of complex shape, hard base, mold scrapping, etc., and achieve the effect of good stability, high cost performance and low cost
- Summary
- Abstract
- Description
- Claims
- Application Information
AI Technical Summary
Problems solved by technology
Method used
Examples
Embodiment 1
[0007] A more stable composite mold base material, the raw materials in the formula are composed by weight percentage: 0.5% modified rubber particles, 10% unsaturated polyester resin, 1% sand, 1% processing aid, 1% flame retardant Agent, 5% foaming agent, 10% stabilizer, 30% lightly burnt powder, at this time can avoid the side shift, but the error of the upper and lower molds will still lead to the scrapping of the mold.
Embodiment 2
[0009] A more stable composite mold base material, the raw materials in the formula are composed by weight percentage: 6% modified rubber particles, 35% unsaturated polyester resin, 10% sand, 3% processing aids, 2.5% flame retardant Agent, 20% foaming agent, 20% stabilizer, 60% lightly burnt powder, at this time can avoid the situation that the mold is scrapped due to the error of the upper and lower molds, but at this time, there may be sideways movement due to the heating and pressing process.
Embodiment 3
[0011] A more stable composite mold base material, the raw materials in the formula are composed by weight percentage: 4% modified rubber particles, 23% unsaturated polyester resin, 5% sand, 1.5% processing aid, 1.25% flame retardant Agent, 13% foaming agent, 15% stabilizer, 45% lightly burnt powder, at this time has excellent stability, can avoid the sideways movement of the mold caused by heating and pressing, and the hardness of the base is relatively low , There will be no upper and lower mold operation errors that directly lead to mold scrapping.
PUM
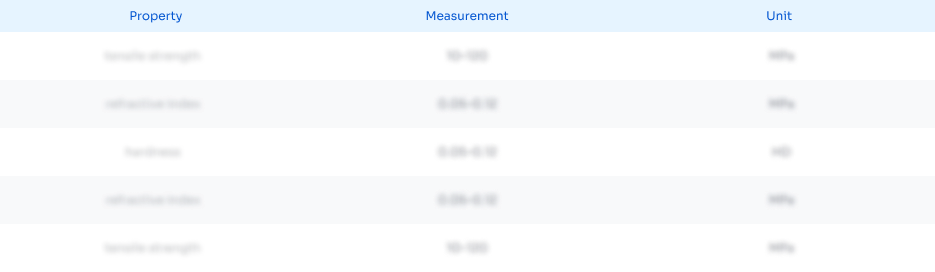
Abstract
Description
Claims
Application Information

- R&D
- Intellectual Property
- Life Sciences
- Materials
- Tech Scout
- Unparalleled Data Quality
- Higher Quality Content
- 60% Fewer Hallucinations
Browse by: Latest US Patents, China's latest patents, Technical Efficacy Thesaurus, Application Domain, Technology Topic, Popular Technical Reports.
© 2025 PatSnap. All rights reserved.Legal|Privacy policy|Modern Slavery Act Transparency Statement|Sitemap|About US| Contact US: help@patsnap.com