Automatic tray transportation method, system and facility
An automatic transportation and pallet technology, applied in the control/adjustment system, non-electric variable control, lifting device, etc., can solve the problems of reducing, inability to realize the autonomous transportation of pallets, and higher space requirements for the transportation channel, reducing the volume and improving the warehouse. Utilization, unmanned and automated effects
- Summary
- Abstract
- Description
- Claims
- Application Information
AI Technical Summary
Problems solved by technology
Method used
Image
Examples
Embodiment Construction
[0048] It should be understood that the specific embodiments described here are only used to explain the present invention, not to limit the present invention.
[0049] The solution of the embodiment of the present invention is mainly: the present invention controls the vehicle body to move to the cargo position through the controller in response to the handling instruction, and locks the target pallet corresponding to the cargo position; controls the protruding of the fork, protruding into the socket of the target tray; after the fork protrudes a preset length, lift the target tray to a preset height, and the preset height is higher than the height of the vehicle body; keep The relative static state between the fork and the target pallet, and move the car body to the bottom of the target pallet; lower the fork until the target pallet falls on the car body, pass the The vehicle body moves the target pallet to the target position corresponding to the transport command, which ca...
PUM
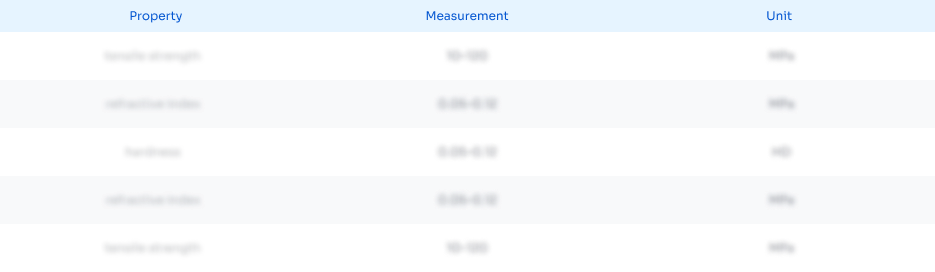
Abstract
Description
Claims
Application Information

- Generate Ideas
- Intellectual Property
- Life Sciences
- Materials
- Tech Scout
- Unparalleled Data Quality
- Higher Quality Content
- 60% Fewer Hallucinations
Browse by: Latest US Patents, China's latest patents, Technical Efficacy Thesaurus, Application Domain, Technology Topic, Popular Technical Reports.
© 2025 PatSnap. All rights reserved.Legal|Privacy policy|Modern Slavery Act Transparency Statement|Sitemap|About US| Contact US: help@patsnap.com