Multi-target optimization method for injection molding process parameters of thin-walled injection molded part
A multi-objective optimization and process parameter technology, applied in the field of injection molding, can solve the problems of energy consumption affecting the molding quality of plastic parts, affecting the molding quality of plastic parts, and flashing of plastic parts, so as to save energy, reduce clamping force, reduce The effect of energy loss
- Summary
- Abstract
- Description
- Claims
- Application Information
AI Technical Summary
Problems solved by technology
Method used
Image
Examples
Embodiment Construction
[0054] The multi-objective optimization method of injection molding process parameters for thin-walled injection molded parts is based on the finite element analysis software Moldflow. First, the orthogonal test design is used on the basis of the simulation of the injection molding process by Moldflow software to minimize warpage, volume shrinkage and maximum clamping. The simulation results of each test group are obtained; then the entropy method is used to determine the weight of each index, and the multi-objective optimization is transformed into a single-objective optimization; then the orthogonal test results are used as a sample set, and the sample set is randomly divided into The training set and the test set are used to establish the best regression model for the training set using the random forest algorithm; finally, the genetic algorithm is used to perform global optimization on the established best regression model to obtain the optimal injection temperature, mold te...
PUM
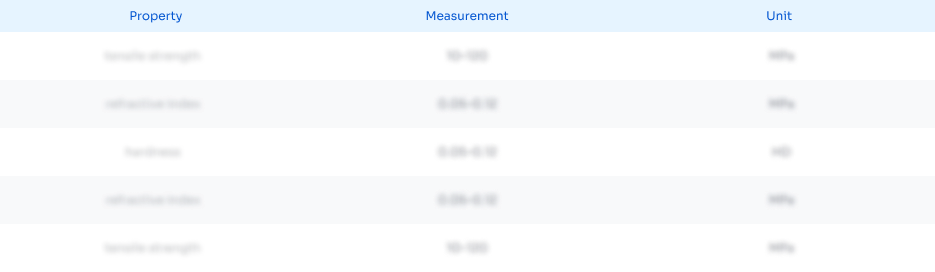
Abstract
Description
Claims
Application Information

- Generate Ideas
- Intellectual Property
- Life Sciences
- Materials
- Tech Scout
- Unparalleled Data Quality
- Higher Quality Content
- 60% Fewer Hallucinations
Browse by: Latest US Patents, China's latest patents, Technical Efficacy Thesaurus, Application Domain, Technology Topic, Popular Technical Reports.
© 2025 PatSnap. All rights reserved.Legal|Privacy policy|Modern Slavery Act Transparency Statement|Sitemap|About US| Contact US: help@patsnap.com