Production process of a cotton-feeling lightweight anti-feather fabric
A kind of anti-feather fabric and production process technology, applied in the direction of protective clothing, fiber type, fabric surface trimming, etc., can solve the problems of weaving difficulties, insufficient air permeability of the fabric, and no direct contact with the human body, etc., to achieve good feather resistance and imitation cotton Effect, overcoming the problem of sanding strips, overcoming the effect of high price and cost
- Summary
- Abstract
- Description
- Claims
- Application Information
AI Technical Summary
Problems solved by technology
Method used
Examples
Embodiment 1
[0031] Fabric preparation
[0032] Gray cloth parameter formulation: the warp and weft yarns of the gray cloth are made of high F-number polyester DTY filaments, the warp and weft yarn fineness is 45D, the warp and weft yarn F-number is not less than 72, the warp density on the machine is 180 threads / inch, and the weft density is 180 threads / inch;
[0033] Warping: divide the warp yarn into 10 parts according to the width of the gray cloth, and each part of the warp yarn is wound onto the warp beam by a section warping machine and a sub-skeining reed, and the speed of the section warping machine is 160m / min;
[0034] Sizing: Sizing the warp beams separately. During sizing, the workshop temperature is 28°C, the humidity is 60%, the temperature of the slurry is 55°C, and the sizing rate is 13%. The size is made of polyacrylate, an environmentally friendly polyester size;
[0035] Doubling: put the processed warp beams on the doubling creel, and wind the warp yarns on each warp b...
Embodiment 2
[0049] Fabric preparation
[0050] Gray cloth parameter formulation: the warp and weft yarns of the gray cloth are made of high F-number polyester DTY filaments, the warp and weft yarn fineness is 75D, the warp and weft yarn F-number is not less than 72, the warp density on the machine is 230 threads / inch, and the weft density is 200 threads / inch;
[0051] Warping: divide the warp yarn into 12 parts according to the width of the gray cloth, and each part of the warp yarn is wound onto the warp beam by a section warping machine and a sub-skeining reed, and the speed of the section warping machine is 180m / min;
[0052] Sizing: Sizing the warp beams separately. When sizing, the temperature of the workshop is 30°C, the humidity is 65%, the temperature of the slurry is 60°C, and the sizing rate is 15%. The size is made of polyacrylate, an environmentally friendly polyester size;
[0053] Doubling: place the processed warp beams on the doubling creel, pass the warp yarns on each war...
PUM
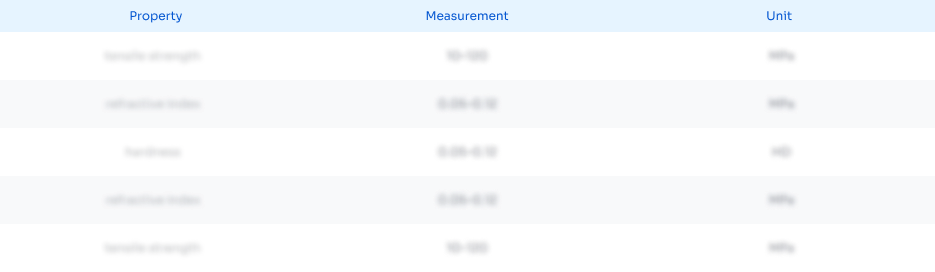
Abstract
Description
Claims
Application Information

- Generate Ideas
- Intellectual Property
- Life Sciences
- Materials
- Tech Scout
- Unparalleled Data Quality
- Higher Quality Content
- 60% Fewer Hallucinations
Browse by: Latest US Patents, China's latest patents, Technical Efficacy Thesaurus, Application Domain, Technology Topic, Popular Technical Reports.
© 2025 PatSnap. All rights reserved.Legal|Privacy policy|Modern Slavery Act Transparency Statement|Sitemap|About US| Contact US: help@patsnap.com