A v-doped ni coated with v-doped nio 3 s 2 Preparation method of core-shell structure
A technology of core-shell structure and nickel foam, which is applied in the field of preparation of composite materials, can solve problems such as poor structural stability, achieve fast reaction kinetics, improve electronic structure, excellent electrocatalytic oxygen evolution and hydrogen evolution performance and stability
- Summary
- Abstract
- Description
- Claims
- Application Information
AI Technical Summary
Problems solved by technology
Method used
Image
Examples
Embodiment 1
[0032] 1) Add 0.2g of vanadium chloride and 0.5g of urea into 25ml of ultrapure water and stir to obtain solution A; Put it in a vinyl fluoride liner and seal it, then put it into a homogeneous reactor for hydrothermal reaction at 135°C for 10h, cool to room temperature and take out the nickel foam, wash it with ultrapure water and absolute ethanol, and dry it in vacuum at 25°C for 4h to obtain NiV-LDH / NF grown on nickel foam in situ using nickel foam as nickel source;
[0033] The nickel foam used was ultrasonically cleaned in acetone for 10 minutes, then ultrasonically cleaned in 2mol / L hydrochloric acid for 15 minutes to remove surface impurities, rinsed alternately with ethanol and deionized water, and then vacuum-dried at 35°C for 3 hours;
[0034] 2) Add 40mg of thioacetamide to 20ml of deionized water to obtain a thioacetamide solution; put the thioacetamide solution and the NiV-LDH / NF obtained in step 1) into a hydrothermal kettle and heat at 128°C Cool to room temper...
Embodiment 2
[0037] 1) Add 0.1g of vanadium chloride and 0.3g of urea into 23ml of ultrapure water and stir to obtain solution A; Put it in a vinyl fluoride liner and seal it, then put it into a homogeneous reaction apparatus and conduct a hydrothermal reaction at 130°C for 12 hours, cool to room temperature and take out the nickel foam, wash it with ultrapure water and absolute ethanol, and dry it in vacuum at 35°C for 3 hours to obtain NiV-LDH / NF grown on nickel foam in situ using nickel foam as nickel source;
[0038] The nickel foam used was ultrasonically cleaned in acetone for 5 minutes, then ultrasonically cleaned in 3mol / L hydrochloric acid for 10 minutes to remove surface impurities, rinsed alternately with ethanol and deionized water, and then vacuum-dried at 25°C for 4 hours;
[0039] 2) Add 40mg of thioacetamide to 25ml of deionized water to obtain a thioacetamide solution; put the thioacetamide solution and the NiV-LDH / NF obtained in step 1) into a hydrothermal kettle and heat...
Embodiment 3
[0042]1) Add 0.15g of vanadium chloride and 0.4g of urea to 20ml of ultrapure water and stir to obtain solution A; Put it in a vinyl fluoride liner and seal it, then put it into a homogeneous reactor for hydrothermal reaction at 125°C for 14h, cool to room temperature and take out the nickel foam, wash it with ultrapure water and absolute ethanol, and dry it in vacuum at 30°C for 3.5h Obtain NiV-LDH / NF grown on nickel foam in situ with nickel foam as nickel source;
[0043] The nickel foam used was ultrasonically cleaned in acetone for 8 minutes, then ultrasonically cleaned in 2.5mol / L hydrochloric acid for 13 minutes to remove surface impurities, rinsed alternately with ethanol and deionized water, and then vacuum-dried at 30°C for 3.5 h;
[0044] 2) Add 40mg of thioacetamide to 20ml of deionized water to obtain a thioacetamide solution; put the thioacetamide solution and the NiV-LDH / NF obtained in step 1) into a hydrothermal kettle and heat at 130°C Cool to room temperatur...
PUM
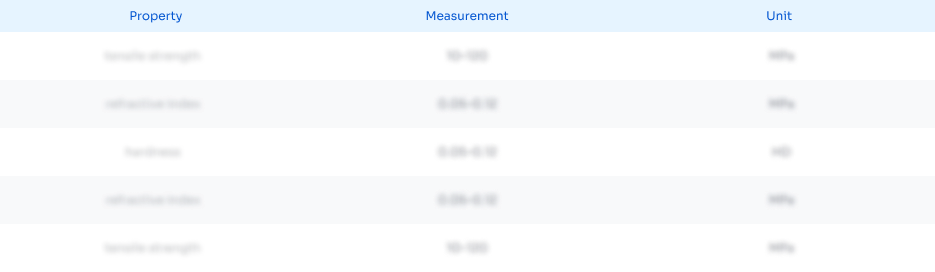
Abstract
Description
Claims
Application Information

- R&D
- Intellectual Property
- Life Sciences
- Materials
- Tech Scout
- Unparalleled Data Quality
- Higher Quality Content
- 60% Fewer Hallucinations
Browse by: Latest US Patents, China's latest patents, Technical Efficacy Thesaurus, Application Domain, Technology Topic, Popular Technical Reports.
© 2025 PatSnap. All rights reserved.Legal|Privacy policy|Modern Slavery Act Transparency Statement|Sitemap|About US| Contact US: help@patsnap.com