Preparation method of super-hydrophobic graphene wind turbine blade surface protective coating material and product thereof
A technology for protective coatings and wind turbine blades, applied in anti-corrosion coatings, anti-fouling/underwater coatings, coatings, etc., can solve problems such as shortened service life of wind turbine blades
- Summary
- Abstract
- Description
- Claims
- Application Information
AI Technical Summary
Problems solved by technology
Method used
Image
Examples
Embodiment 1
[0025] Put 0.6 g styrene and 2.5 g trifluorooctyl methacrylate monomer in a 100 mL three-necked flask and mix evenly, add 0.03 g azobisisobutylcyanide to the system, and the reaction temperature is 70 o C. The reaction system continued for 10 hours to synthesize styrene / tridecafluorooctyl methacrylate copolymer. Dissolve the styrene / tridecafluorooctyl methacrylate copolymer with an appropriate amount of tetrahydrofuran, precipitate with methanol, wash repeatedly, and dry the precipitate at a constant temperature (60 oC) to a constant weight to obtain a fluorine-containing acrylate binary copolymer for use. Add 1.0 g of flake graphite, 1.2 g of potassium nitrate and 46 mL of concentrated sulfuric acid into a 500 mL four-neck flask and mix evenly. Slowly add 6.0 g of potassium permanganate in an ice-water bath and stir. Then the temperature was raised to 40° C., and the reaction was stirred at high speed for 6 hours. Slowly add 80 mL of distilled water to the reaction system a...
Embodiment 2
[0027] Put 1.1 g of styrene and 2.0 g of trifluorooctyl methacrylate monomer in a 100 mL three-necked flask and mix evenly, add 0.03 g of azobisisobutylcyanide to the system, and the reaction temperature is 70 o C, the reaction system continued for 12 hours to synthesize styrene / tridecafluorooctyl methacrylate copolymer. Dissolve the synthesized styrene / tridecafluorooctyl methacrylate copolymer with an appropriate amount of tetrahydrofuran, precipitate with methanol, wash repeatedly, and dry the precipitate at a constant temperature (60 o C) to a constant weight to obtain a fluorine-containing acrylate binary copolymer for use. Add 1.0 g of flake graphite, 1.2 g of potassium nitrate and 46 mL of concentrated sulfuric acid into a 500 mL four-neck flask and mix evenly. Slowly add 6.0 g of potassium permanganate in an ice-water bath and stir. Then the temperature was raised to 40° C., and the reaction was stirred at high speed for 6 hours. Slowly add 80 mL of distilled water to...
Embodiment 3
[0029] Put 2.2 g of styrene and 1.0 g of trifluorooctyl methacrylate monomer in a 100 mL three-necked flask and mix evenly, add 0.03 g of azobisisobutylcyanide to the system, and the reaction temperature is 70 o C, the reaction system continued for 14 hours to synthesize styrene / tridecafluorooctyl methacrylate copolymer. Dissolve styrene / tridecafluorooctyl methacrylate copolymer with an appropriate amount of tetrahydrofuran, precipitate with methanol, wash repeatedly, and dry the precipitate at constant temperature (60 o C) to a constant weight to obtain a fluorine-containing acrylate binary copolymer for use. Add 1.0 g of flake graphite, 1.2 g of potassium nitrate and 46 mL of concentrated sulfuric acid into a 500 mL four-neck flask and mix evenly. Slowly add 6.0 g of potassium permanganate in an ice-water bath and stir. Then the temperature was raised to 40° C., and the reaction was stirred at high speed for 6 hours. Slowly add 80 mL of distilled water to the reaction syst...
PUM
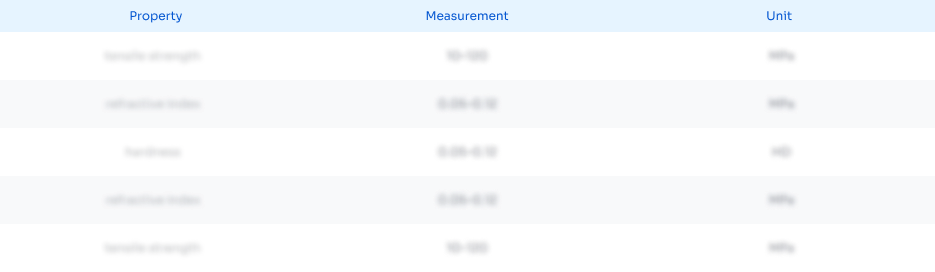
Abstract
Description
Claims
Application Information

- R&D
- Intellectual Property
- Life Sciences
- Materials
- Tech Scout
- Unparalleled Data Quality
- Higher Quality Content
- 60% Fewer Hallucinations
Browse by: Latest US Patents, China's latest patents, Technical Efficacy Thesaurus, Application Domain, Technology Topic, Popular Technical Reports.
© 2025 PatSnap. All rights reserved.Legal|Privacy policy|Modern Slavery Act Transparency Statement|Sitemap|About US| Contact US: help@patsnap.com