Full-process cyclic dyeing system and process and application thereof
A dyeing system and full-process technology, applied in the field of energy saving and emission reduction in printing and dyeing, can solve problems such as waste, loss of resources, and increased processing difficulty, achieving high removal rate and reducing processing difficulty
- Summary
- Abstract
- Description
- Claims
- Application Information
AI Technical Summary
Problems solved by technology
Method used
Image
Examples
Embodiment 1
[0044] What this embodiment discloses is a kind of process that utilizes above-mentioned full-process cyclic dyeing system to carry out full-process cyclic dyeing of cotton textiles, and adopts reactive dyes to dye.
[0045] Ordinary dyeing process:
[0046] The dyeing prescription is: cotton fabric: 2kg, bath ratio 1:10, reactive black WNN: 6% (owf), sodium chloride: 60g / L, color-fixing alkali XA: 3g / L, soaping agent XA: 2g / L L; the dyeing process is: dyeing (60℃×60min)→neutralization (HAc:0.5g / L, 80℃×15min)→soaping (80℃×15min)→hot water washing (80℃×15min)→warm water washing (60℃×15min) → cold water washing (10min);
[0047] Recycling treatment:
[0048] After dyeing, the dyeing wastewater passes through the dye capture separator (molecular weight cut-off 1000 Daltons) to obtain dyeing circulating water and temporarily stores it in the dyeing pool for use. The membrane dye capture separator and the reverse osmosis membrane salt concentration separator are temporarily stor...
Embodiment 2
[0057] What this embodiment discloses is a kind of process that utilizes the above-mentioned full-process cyclic dyeing system to carry out full-process cyclic dyeing of polyester fabrics, and adopts disperse dyes for dyeing.
[0058] Ordinary dyeing process:
[0059] The dyeing prescription is: polyester fabric: 2kg, bath ratio 1:10, disperse black ECT: 3% (owf), HAc: 0.5g / L, high temperature leveling agent XA: 1g / L, reducing cleaning agent XA: 3g / L L; the dyeing process is: dyeing (1-2°C / min heating up to 130°C×45min, cooling down to 80°C)→reduction cleaning (80°C×15min)→hot washing (80°C×15min)→warm water washing (60°C ×15min) → cold water wash (10min);
[0060] Recycling treatment:
[0061] After dyeing, the dyeing wastewater passes through the extraction resin capture separator to obtain dyeing circulating water and temporarily stores it in the dyeing pool for use. The waste water from reduction cleaning, hot water washing, warm water washing, and cold water washing is ...
Embodiment 3
[0070] What this embodiment discloses is a kind of process that utilizes the above-mentioned full-process cyclic dyeing system to carry out full-process cyclic dyeing of acrylic yarn, and adopts cationic dyes for dyeing.
[0071] Ordinary dyeing process:
[0072] The dyeing prescription is: acrylic yarn: 2kg, bath ratio 1:10, cationic light gray: XGL golden 0.06% + XGRL red 0.04% + XBL blue 0.07% (owf), leveling agent 1227: 3g / L; The process is: dyeing (1-2°C / min heating up to 98°C×30min, cooling down to 80°C) → warm water washing (60°C×15min) → cold water washing (10min);
[0073] Recycling treatment:
[0074] After dyeing, the dyeing wastewater passes through the dyeing residue decolorization separator to obtain dyeing circulating water and temporarily stores it in the dyeing pool for use. The wastewater washed with warm water and cold water is respectively passed through the dyeing residue decolorization separator and the nanofiltration membrane salt concentration separato...
PUM
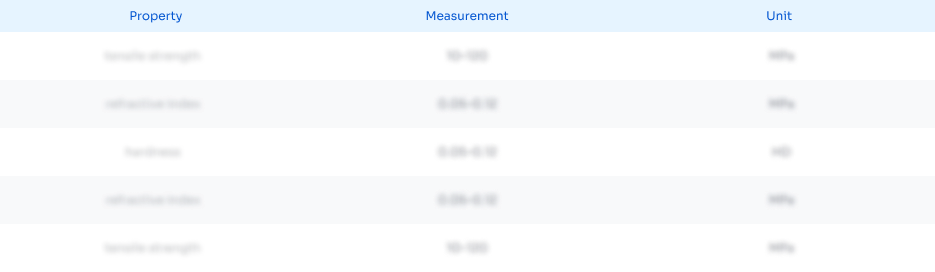
Abstract
Description
Claims
Application Information

- R&D
- Intellectual Property
- Life Sciences
- Materials
- Tech Scout
- Unparalleled Data Quality
- Higher Quality Content
- 60% Fewer Hallucinations
Browse by: Latest US Patents, China's latest patents, Technical Efficacy Thesaurus, Application Domain, Technology Topic, Popular Technical Reports.
© 2025 PatSnap. All rights reserved.Legal|Privacy policy|Modern Slavery Act Transparency Statement|Sitemap|About US| Contact US: help@patsnap.com