Slurry mixing process of lithium ion battery slurry
A lithium-ion battery and slurry technology, applied in secondary batteries, battery electrodes, circuits, etc., can solve the problems affecting the uniformity and fluidity of the slurry, the performance of the lithium-ion battery, and the utilization rate of raw materials, etc. Contact and dispersion effects, enhanced kneading and shearing effects, and improved pulp mixing efficiency
- Summary
- Abstract
- Description
- Claims
- Application Information
AI Technical Summary
Problems solved by technology
Method used
Examples
Embodiment 1
[0026] Embodiment 1: A kind of slurry mixing process of positive electrode slurry of lithium ion battery, calculated by weight ratio, active material is nickel cobalt lithium manganese oxide Li(NiCoMn)O of 53 parts 2 2 parts of Ketjen Black ECP and 3 parts of conductive carbon black super-P as the conductive agent, 2 parts of modified polyvinylidene fluoride PVDF as the binder, and 40 parts of N-methylpyrrolidone NMP as the solvent, It includes the following steps:
[0027] 1. Glue making: Stir the amount of PVDF and 50-70% (can be 20 parts, 24 parts, 26 parts, 28 parts, etc.) of NMP solvent in a double planetary mixer to make glue. The revolution speed of the planetary mixer is any value between 25-60 rpm, preferably any value between 30-50 rpm, and the dispersion speed is any value between 1000-4500 rpm, preferably 1500 Any value in ~3000 rev / min, any value in the stirring time of 180-240 minutes.
[0028] 2. Dry mixing: the amount of nickel-cobalt lithium manganese oxide ...
Embodiment 2
[0044] Embodiment 2: A slurry mixing process of graphite mixed with amorphous carbon negative electrode slurry in a power lithium ion battery, the formula is as follows: calculated by weight ratio, including 34.5 parts of active material artificial graphite, 15.5 parts of active material hard carbon, 1 part of binder CMC, 2 parts of conductive agent Super-P and 1 part of binder SBR and 46 parts of deionized water solvent. It includes the following steps:
[0045] 1. Gluing: Mix the amount of CMC and 50-70% of the total amount (it can be 23 parts, 27.6 parts, 32.2 parts, 29.9 parts, etc.) of deionized water solvent in a double planetary mixer to make glue. Control the revolution speed of the double planetary mixer at any value from 25 to 60 rpm, preferably any value from 30 to 50 rpm, and the dispersion speed to any value from 1000 to 4500 rpm, preferably Any value in 1500~3000 rev / min, stirring time in any value in 180-240 minutes.
[0046] 2. Dry mixing: pre-mix the stated ...
PUM
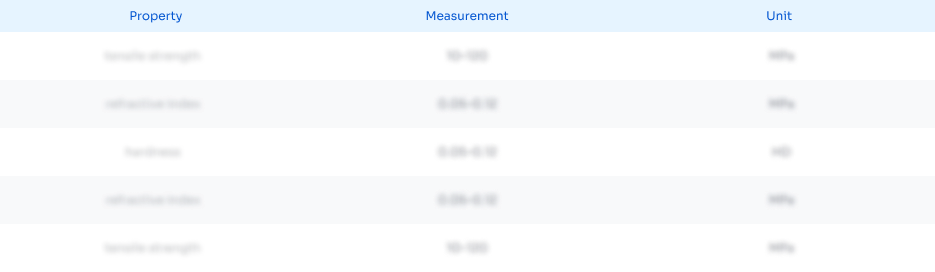
Abstract
Description
Claims
Application Information

- R&D
- Intellectual Property
- Life Sciences
- Materials
- Tech Scout
- Unparalleled Data Quality
- Higher Quality Content
- 60% Fewer Hallucinations
Browse by: Latest US Patents, China's latest patents, Technical Efficacy Thesaurus, Application Domain, Technology Topic, Popular Technical Reports.
© 2025 PatSnap. All rights reserved.Legal|Privacy policy|Modern Slavery Act Transparency Statement|Sitemap|About US| Contact US: help@patsnap.com