Special halogen-free flame-retardant synergistic masterbatch for modification of nylon resin and preparation method of halogen-free flame-retardant synergistic masterbatch
A functional masterbatch, flame retardant and synergistic technology, applied in the field of plastic modification processing, can solve the problems of weak interface adhesion, poor heat resistance and thermal stability, low fluidity, etc., and achieve enhanced compactness and structural stability. resistance, excellent heat resistance and thermal stability, the effect of increasing the thermal decomposition temperature
- Summary
- Abstract
- Description
- Claims
- Application Information
AI Technical Summary
Problems solved by technology
Method used
Image
Examples
Embodiment 1
[0033] A special halogen-free flame retardant synergistic functional masterbatch for nylon resin modification, the quality ratio of raw materials is as follows:
[0034] Multiple composite coated aluminum diethylphosphinate 65.0kg Anhydrous zinc borate 20.0kg Nylon 6 resin 10.0kg Four-arm star nylon 6 resin 3.0kg Styrene-acrylonitrile copolymer coated PTFE 1.0 kg Zinc stearate 500.0 g OP wax 500.0 g
[0035] The preparation method of the multi-compound coated aluminum diethylphosphinate used in the above-mentioned nylon resin modified special halogen-free flame retardant synergistic functional masterbatch is as follows:
[0036] Add 230 L of absolute ethanol, 120 kg of aluminum diethylphosphinate, 7 kg of aluminum sol, and 1 kg of zinc oxide sol into the enamel reaction kettle with a stirring and temperature control device, stir evenly and add to 40°C, and then Add dropwise ammonia water with a mass percentage of 10.0wt.%,...
Embodiment 2
[0039] A special halogen-free flame retardant synergistic functional masterbatch for nylon resin modification, the quality ratio of raw materials is as follows:
[0040] Multiple composite coated aluminum diethylphosphinate 55.0kg Anhydrous zinc borate 30.0kg Nylon 6 resin 8.5 kg Three-arm star nylon 6 resin 5.0 kg Styrene-acrylonitrile copolymer coated PTFE 500.0 g Aluminum stearate 700.0 g E wax 300.0 g
[0041] The preparation method of the multi-compound coated aluminum diethylphosphinate used in the above-mentioned nylon resin modified special halogen-free flame retardant synergistic functional masterbatch is as follows:
[0042] Add 230L of absolute ethanol, 120kg of aluminum diethylphosphinate, 8 kg of aluminum sol, and 1.5 kg of zinc oxide sol into the enamel reaction kettle with a stirring and temperature control device, stir evenly and add to 35°C, then drop at a uniform speed Add ammonia water with a mass percent...
Embodiment 3
[0045] A special halogen-free flame retardant synergistic functional masterbatch for nylon resin modification, the quality ratio of raw materials is as follows:
[0046] Multiple composite coated aluminum diethylphosphinate 60.0 kg Anhydrous zinc borate 28.0 kg Nylon 6 resin 8.0 kg Six-arm star nylon 6 resin 2.0 kg Styrene-acrylonitrile copolymer coated PTFE 700.0 g Magnesium stearate 1.0 kg Ethylene-vinyl acetate copolymer wax 300.0 g
[0047] The preparation method of the multi-compound coated aluminum diethylphosphinate used in the above-mentioned nylon resin modified special halogen-free flame retardant synergistic functional masterbatch is as follows:
[0048] Add 230 L of absolute ethanol, 120 kg of aluminum diethylphosphinate, 7.5 kg of aluminum sol, and 2 kg of zinc oxide sol into the enamel reaction kettle with a stirring and temperature control device, stir well and add to 37°C, and then Quickly add ammonia water...
PUM
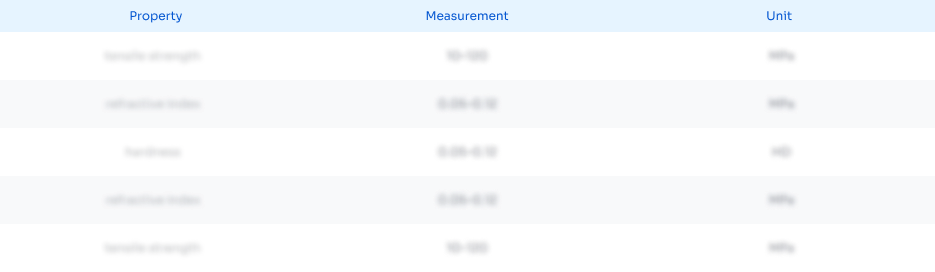
Abstract
Description
Claims
Application Information

- Generate Ideas
- Intellectual Property
- Life Sciences
- Materials
- Tech Scout
- Unparalleled Data Quality
- Higher Quality Content
- 60% Fewer Hallucinations
Browse by: Latest US Patents, China's latest patents, Technical Efficacy Thesaurus, Application Domain, Technology Topic, Popular Technical Reports.
© 2025 PatSnap. All rights reserved.Legal|Privacy policy|Modern Slavery Act Transparency Statement|Sitemap|About US| Contact US: help@patsnap.com