Environment-friendly wear-resistant cable
An environmentally friendly, cable technology, used in insulated cables, cables, circuits, etc., can solve the problems of poor wear resistance of cable skin, difficult to distinguish conductors, poor protection, etc., to achieve good adhesion and aging resistance, fast vulcanization speed , The effect of good anti-scorch performance
- Summary
- Abstract
- Description
- Claims
- Application Information
AI Technical Summary
Problems solved by technology
Method used
Image
Examples
Embodiment 1
[0053] Embodiment 1, the materials used for the wear-resistant rubber layer 4 include by weight:
[0054] 40 parts of hydrogenated nitrile rubber, 20 parts of polyvinyl chloride resin, 10 parts of natural rubber, 12 parts of ethylene-octene copolymer, 5 parts of silane coupling agent, 5 parts of modified PP, 0.5 parts of neoprene, 1 part of sulfur , 2 parts of zinc oxide, 2 parts of magnesium oxide, 2.5 parts of magnesium hydroxide inorganic flame retardant, 1 part of antimony trioxide, 10 parts of carbon microspheres, 5 parts of cast stone powder, 5 parts of nano-carbon black, 15 parts of nano-clay, 1 part of CPE special stabilizer, 5 parts of trioctyl trimellitate, 0.5 parts of paraffin, 1.5 parts of stearic acid, 1 part of pressure-sensitive microcapsules, 1 part of calcium zinc stabilizer, dodecyl dimethyl beet 2 parts of alkali, 1 part of nano silicon dioxide particles.
[0055] The materials used for the wear-resistant rubber layer 4 specifically include the following pro...
Embodiment 2
[0061] Embodiment 2, the materials used for the wear-resistant rubber layer 4 include by weight:
[0062] 45 parts of hydrogenated nitrile rubber, 25 parts of polyvinyl chloride resin, 14 parts of natural rubber, 16 parts of ethylene-octene copolymer, 9 parts of silane coupling agent, 8 parts of modified PP, 0.8 parts of neoprene, 1.5 parts of sulfur , 3.5 parts of zinc oxide, 3 parts of magnesium oxide, 3 parts of magnesium hydroxide inorganic flame retardant, 1.5 parts of antimony trioxide, 15 parts of carbon microspheres, 7.5 parts of cast stone powder, 10 parts of nano-carbon black, 17.5 parts of nano-clay, 1.5 parts of CPE special stabilizer, 6 parts of trioctyl trimellitate, 1 part of paraffin, 2 parts of stearic acid, 2.5 parts of pressure-sensitive microcapsules, 1.5 parts of calcium zinc stabilizer, dodecyl dimethyl beet 2.5 parts of alkali, 2.5 parts of nano silicon dioxide particles;
[0063] The materials used for the wear-resistant rubber layer 4 specifically inc...
Embodiment 3
[0069] Embodiment 3, the materials used for the wear-resistant rubber layer 4 include by weight:
[0070] 50 parts of hydrogenated nitrile rubber, 30 parts of polyvinyl chloride resin, 18 parts of natural rubber, 20 parts of ethylene-octene copolymer, 13 parts of silane coupling agent, 10 parts of modified PP, 1 part of neoprene, 2 parts of sulfur , 5 parts of zinc oxide, 4 parts of magnesium oxide, 4 parts of magnesium hydroxide inorganic flame retardant, 2 parts of antimony trioxide, 20 parts of carbon microspheres, 10 parts of cast stone powder, 15 parts of nano-carbon black, 20 parts of nano-clay, 2 parts of CPE special stabilizer, 7 parts of trioctyl trimellitate, 1.5 parts of paraffin, 3 parts of stearic acid, 5 parts of pressure-sensitive microcapsules, 2 parts of calcium zinc stabilizer, dodecyl dimethyl beet 3 parts of alkali, 5 parts of nano silicon dioxide particles;
[0071] The materials used for the wear-resistant rubber layer 4 specifically include the followin...
PUM
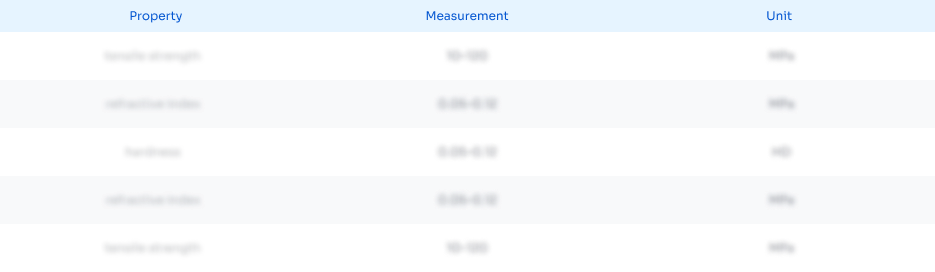
Abstract
Description
Claims
Application Information

- R&D Engineer
- R&D Manager
- IP Professional
- Industry Leading Data Capabilities
- Powerful AI technology
- Patent DNA Extraction
Browse by: Latest US Patents, China's latest patents, Technical Efficacy Thesaurus, Application Domain, Technology Topic, Popular Technical Reports.
© 2024 PatSnap. All rights reserved.Legal|Privacy policy|Modern Slavery Act Transparency Statement|Sitemap|About US| Contact US: help@patsnap.com