Anti-swing driving control method for crane
A crane and anti-sway technology, which is applied to load hanging components, transportation and packaging, complex mathematical operations, etc., can solve problems such as low control accuracy, limited adjustment effect, and slow response speed.
- Summary
- Abstract
- Description
- Claims
- Application Information
AI Technical Summary
Problems solved by technology
Method used
Image
Examples
Embodiment 1
[0064] like Figure 1-7 As shown, the crane anti-sway driving control method of the present invention includes the following steps:
[0065] Step 1. Input variables through sensors, including car position x, speed Load swing angle θ and swing angular acceleration
[0066] Step 2, according to the formula will input the variable x θ Input the sliding mode control module, and introduce the output of the sliding mode control module into the type II fuzzy system for processing, among which, the s 1 ,s 2 Indicates the first-level sliding plane composed of two groups of states of horizontal displacement and swing angle, c 1 , c 2 Indicates the input adjustment parameters, α and β respectively represent the adjustment parameters of the first-level sliding function, e represents the difference between the current position x and the reference position x* in the horizontal direction, is the speed error of the horizontal motion of the crane;
[0067] Step 3, according...
PUM
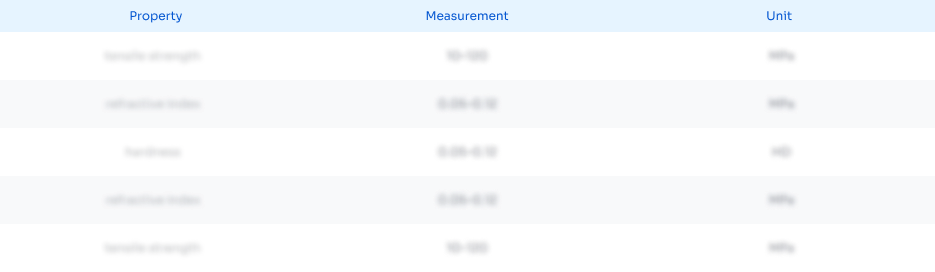
Abstract
Description
Claims
Application Information

- R&D
- Intellectual Property
- Life Sciences
- Materials
- Tech Scout
- Unparalleled Data Quality
- Higher Quality Content
- 60% Fewer Hallucinations
Browse by: Latest US Patents, China's latest patents, Technical Efficacy Thesaurus, Application Domain, Technology Topic, Popular Technical Reports.
© 2025 PatSnap. All rights reserved.Legal|Privacy policy|Modern Slavery Act Transparency Statement|Sitemap|About US| Contact US: help@patsnap.com