Vibrating wire feeding welding device based on linear motor
A linear motor and welding device technology, applied in tin feeding devices, welding equipment, metal processing equipment, etc., can solve the problems of complex mechanical structure, overall cumbersome and complex, inconvenient control, etc., to reduce splash generation and heat input. The effect of improving the quality of welding seam
- Summary
- Abstract
- Description
- Claims
- Application Information
AI Technical Summary
Problems solved by technology
Method used
Image
Examples
Embodiment 1
[0022] See attached structure Figure 1-Figure 5 .
[0023] Including wire feeding box 1, linear motor unit 2, insulating plate 3, wire feeding pipe assembly 4, connector 5, wire feeding machine unit 6, welding wire 7 and welding wire reel 8, wire feeding box 1 includes box side frame 101. The box chassis 102, the first box side wall 103 and the second box side wall 104. The linear motor unit 2 is composed of a stator 201 and a mover 202. It is characterized in that: the box side frame 101, the first The box body side wall 103 and the second box body side wall 104 are fixed on the box body chassis 102, the box body side frame 101 links to each other with the first box body side wall 103 and is perpendicular to the box body chassis 102, the first box body side wall 103 and the second box side wall 104 are opposite and vertical to the box chassis 102, such as image 3 As shown, the mover 202 is located above the stator 201, a slider is provided between the mover 202 and the st...
PUM
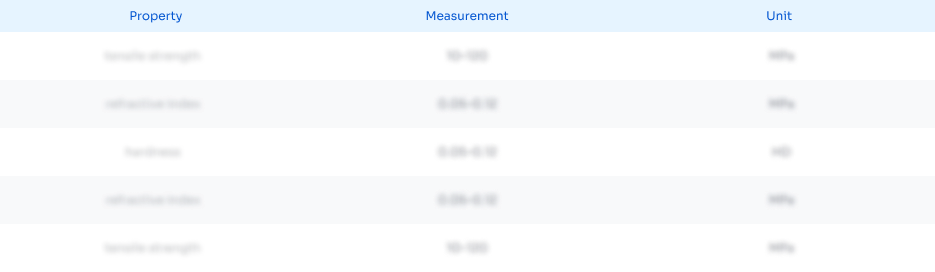
Abstract
Description
Claims
Application Information

- R&D Engineer
- R&D Manager
- IP Professional
- Industry Leading Data Capabilities
- Powerful AI technology
- Patent DNA Extraction
Browse by: Latest US Patents, China's latest patents, Technical Efficacy Thesaurus, Application Domain, Technology Topic, Popular Technical Reports.
© 2024 PatSnap. All rights reserved.Legal|Privacy policy|Modern Slavery Act Transparency Statement|Sitemap|About US| Contact US: help@patsnap.com