Double-nozzle-scanning inclined spray type cylinder blank injection moulding device
An injection forming and cylindrical blank technology, which is applied in the field of dual-nozzle scanning oblique injection cylindrical blank injection forming devices, can solve the problems of large bending moment, environmental impact, material waste, etc., to improve operation stability, reduce material waste, reduce The effect of exhaust pollution
- Summary
- Abstract
- Description
- Claims
- Application Information
AI Technical Summary
Problems solved by technology
Method used
Image
Examples
Embodiment Construction
[0013] As shown in the figure, the dual-nozzle scanning oblique-spray cylindrical billet injection molding device includes a deposition chamber 1, a leak bag 2 for storing liquid metal and an atomizing nozzle 3 connected to the bottom of the leak bag are arranged on the top of the deposition chamber, and the deposition The chamber is provided with a rotatable deposition base 4; the deposition base is located in the center of the deposition chamber and its axis of rotation is in the vertical direction, the atomizing nozzle 3 is located above the deposition base side, and the spray nozzle of the atomizing nozzle 3 is controlled by a swing mechanism to swing back and forth ; There are two atomizing nozzles, and the distances between the two nozzles and the axis line of the deposition base are not equal.
[0014] The bottom outlet of the deposition chamber 1 is connected with a powder collecting box 5, the powder collecting box is connected with an exhaust fan 6 through an exhaust ...
PUM
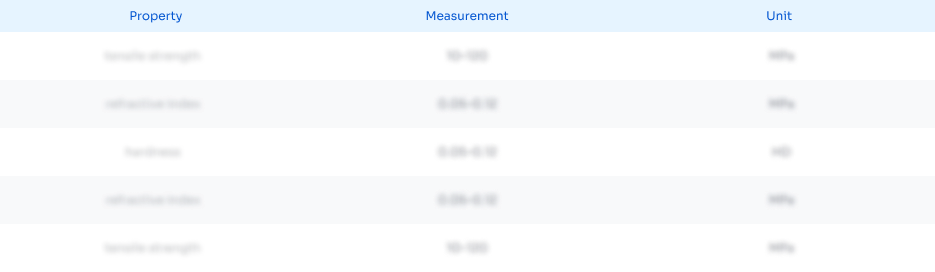
Abstract
Description
Claims
Application Information

- R&D
- Intellectual Property
- Life Sciences
- Materials
- Tech Scout
- Unparalleled Data Quality
- Higher Quality Content
- 60% Fewer Hallucinations
Browse by: Latest US Patents, China's latest patents, Technical Efficacy Thesaurus, Application Domain, Technology Topic, Popular Technical Reports.
© 2025 PatSnap. All rights reserved.Legal|Privacy policy|Modern Slavery Act Transparency Statement|Sitemap|About US| Contact US: help@patsnap.com