Fischer-Tropsch synthesis catalyst and preparation method and application thereof
A Fischer-Tropsch synthesis and catalyst technology, which is used in catalyst activation/preparation, chemical instruments and methods, preparation of liquid hydrocarbon mixtures, etc., can solve the problems of poor product selectivity, unfeasible, low activity, etc., and achieve mild production conditions. , low production cost, and the effect of improving the structure
- Summary
- Abstract
- Description
- Claims
- Application Information
AI Technical Summary
Problems solved by technology
Method used
Image
Examples
Embodiment 1
[0038] 2000 kg Fe(NO 3 ) 3 9H 2 O, 36 kilograms of 50wt% Mn (NO 3 ) 3 Aqueous solution, 10.65 kg Cr(NO 3 ) 3 ·3H 2 O and 6.3 kg of Zn(NO 3 ) 2 ·6H 2 O was dissolved in 1050 kg of deionized water, and after fully dissolved, SiO was added to the mixed salt solution 2 45 kg of silica sol with a content of 30 wt%, Al 2 o 3 Content is 1.2 kilograms of aluminum sols of 25wt%, this solution is warmed up to 50 ℃ under stirring, and the total concentration of nitrate in the gained mixed solution is 12.22wt%, and the weight ratio of each component in the described mixed salt solution is Fe: Mn :Cr:Zn:SiO 2 :Al 2 o 3 =100:2.0:0.5:0.5:4.88:0.11.
[0039] Prepare 10.0wt% ammonia solution at the same time and heat up to 30°C. Preset 1500 kg of deionized water in the precipitation tank and preheat it to 50°C. After the temperature rises to the set temperature, add the salt solution and ammonia solution Co-current co-precipitation, keeping the temperature of the slurry in the ...
Embodiment 2
[0043] 2000 kg Fe(NO 3 ) 3 9H 2 O, 324 kg of 50wt% Mn (NO 3 ) 3 Aqueous solution, 127.5 kg Cr(NO 3 ) 3 ·3H 2 O and 201.5 kg of Zn(NO 3 ) 2 ·6H 2 O was dissolved in 1360 kg of deionized water, and after fully dissolved, Al was added to the mixed salt solution 2 o 3 Content is 24.0 kilograms of silica sols of 25.0wt%, this solution is warmed up to 90 ℃ under stirring, and the total concentration of nitrate in the gained mixed solution is 39.6wt%, and the weight ratio of each component in the described salt solution is Fe: Mn :Cr:Zn:Al 2 o 3 =100:20.0:5.0:15.0:2.0.
[0044] Prepare 20.0wt% ammonia solution at the same time and heat up to 60°C. Preset 1500 kg of deionized water in the precipitation tank and preheat to 90°C. After the temperature rises to the set temperature, add the salt solution and ammonia solution For co-current co-precipitation, the temperature of the slurry in the precipitation tank is kept at 90° C., the pH of the mixed synthetic slurry is 9.0±...
Embodiment 3
[0048] 2000 kg Fe(NO 3 ) 3 9H 2 O, 270 kg of 50wt% Mn (NO 3 ) 3 Aqueous solution, 127.5 kg Cr(NO 3 ) 3 ·3H 2 O is dissolved in 2500 kilograms of deionized water, after fully dissolving, this solution is warmed up to 80 ℃ under stirring, and the total concentration of nitrate in the gained mixed salt solution is 29.5wt%, and the weight ratio of each component in this salt solution is Fe:Mn:Cr=100:15.0:6.0.
[0049] Prepare 12.5wt% ammonia solution at the same time and heat up to 40°C. Preset 1500 kg of deionized water in the precipitation tank and preheat it to 80°C. After the temperature rises to the set temperature, add the salt solution and ammonia solution For co-precipitation, the temperature of the slurry in the precipitation tank is kept at 80° C., the pH of the mixed synthetic slurry is 8.5±0.3, and the mixing and co-precipitation process is completed within 30 minutes. Leave to age for 30 minutes.
[0050] The aged slurry was washed with deionized water until ...
PUM
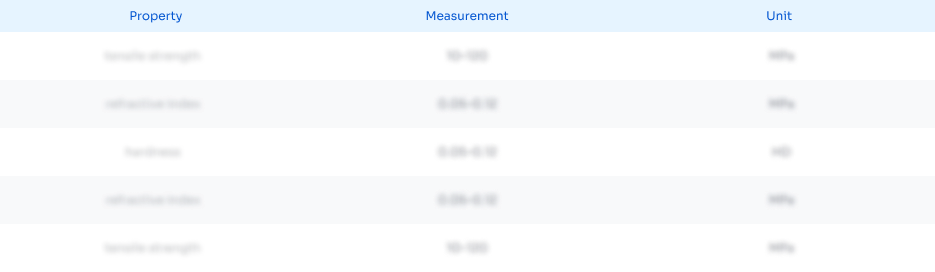
Abstract
Description
Claims
Application Information

- Generate Ideas
- Intellectual Property
- Life Sciences
- Materials
- Tech Scout
- Unparalleled Data Quality
- Higher Quality Content
- 60% Fewer Hallucinations
Browse by: Latest US Patents, China's latest patents, Technical Efficacy Thesaurus, Application Domain, Technology Topic, Popular Technical Reports.
© 2025 PatSnap. All rights reserved.Legal|Privacy policy|Modern Slavery Act Transparency Statement|Sitemap|About US| Contact US: help@patsnap.com