Large-area fabric embossing device and process
A large-area, cloth technology, applied in textile decoration, textile and papermaking, etc., to achieve the effect of improving production efficiency, efficient heating, manufacturing and use costs
- Summary
- Abstract
- Description
- Claims
- Application Information
AI Technical Summary
Problems solved by technology
Method used
Image
Examples
Embodiment 1
[0051] Large-area fabric embossing process, including the following process steps:
[0052] Step A, heating the silicone material to a fluid state and then pouring it into the groove of the lower mold;
[0053] Step B, laying the fabric on the lower mold, and ensuring that the fabric completely covers the groove of the lower mold;
[0054] Step C, after the upper mold and the lower mold are combined, they are sent to the hot molding mechanism for hot compression molding. The pressing pressure between the upper mold and the lower mold is 30 tons / square meter, and the temperature of the hot molding mechanism is 180 degrees Celsius. The time is 50 seconds;
[0055] Step D, send the upper mold and the lower mold in the aligned state to the cold molding press mechanism for cooling treatment, the cooling treatment is to press the soft raw materials in the upper mold and the lower mold to cool and shape, and the pressing between the upper mold and the lower mold The joint pressure ...
Embodiment 2
[0058] Large-area fabric embossing process, including the following process steps:
[0059] Step A, heating the silicone material to a fluid state and then pouring it into the groove of the lower mold;
[0060] Step B, laying the fabric on the lower mold, and ensuring that the fabric completely covers the groove of the lower mold;
[0061] Step C, after the upper mold and the lower mold are combined, they are sent to the hot molding mechanism for hot pressing. The pressing pressure between the upper mold and the lower mold is 40 tons / square meter, and the temperature of the hot molding mechanism is 260 degrees Celsius. The time is 70 seconds;
[0062] Step D, send the upper mold and the lower mold in the aligned state to the cold mold pressing mechanism for cooling treatment, the cooling treatment is to press the soft raw materials in the upper mold and the lower mold to cool and shape, and the pressing between the upper mold and the lower mold The joint pressure is 2 tons / s...
Embodiment 3
[0065] Large-area fabric embossing process, including the following process steps:
[0066] Step A, heating the PVC material to a fluid state and then pouring it into the groove of the lower mold;
[0067] Step B, laying the fabric on the lower mold, and ensuring that the fabric completely covers the groove of the lower mold;
[0068] Step C, the upper mold and the lower mold are combined and then sent to the hot molding mechanism for hot compression molding. The pressing pressure between the upper mold and the lower mold is 30 tons / square meter, and the temperature of the hot molding mechanism is 200 degrees Celsius. The time is 50 seconds;
[0069] Step D, send the upper mold and the lower mold in the aligned state to the cold mold pressing mechanism for cooling treatment, the cooling treatment is to press the soft raw materials in the upper mold and the lower mold to cool and shape, and the pressing between the upper mold and the lower mold The joint pressure is 1 ton / squ...
PUM
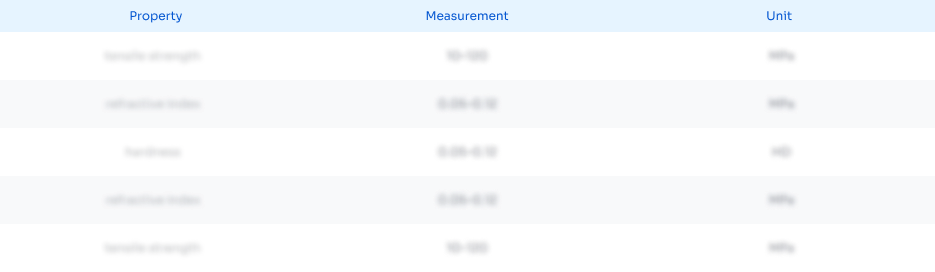
Abstract
Description
Claims
Application Information

- R&D
- Intellectual Property
- Life Sciences
- Materials
- Tech Scout
- Unparalleled Data Quality
- Higher Quality Content
- 60% Fewer Hallucinations
Browse by: Latest US Patents, China's latest patents, Technical Efficacy Thesaurus, Application Domain, Technology Topic, Popular Technical Reports.
© 2025 PatSnap. All rights reserved.Legal|Privacy policy|Modern Slavery Act Transparency Statement|Sitemap|About US| Contact US: help@patsnap.com