A method for preparing light-burned magnesia by a magnesite cracking method
A technology of lightly burning magnesia and magnesite, which is applied in chemical instruments and methods, inorganic chemistry, energy input, etc., and can solve problems such as limited sales, waste of resources, and limited carbon dioxide
- Summary
- Abstract
- Description
- Claims
- Application Information
AI Technical Summary
Problems solved by technology
Method used
Image
Examples
Embodiment approach
[0034] (1) Fill 2Kg of magnesite powder (200 mesh) in a fluidized bed with a diameter of 230mm, start the electric heating device, raise the temperature, feed in electrically heated carbon dioxide gas, and stabilize the fluidization until the temperature of the fluidized bed reaches 1000°C .
[0035] (2) After the magnesite powder is cracked, the magnesium oxide powder and carbon dioxide enter the cyclone separator with the airflow, the outlet temperature of the carbon dioxide is 750°C-850°C, and the temperature of the magnesium oxide powder is 800-900°C.
[0036] (3) The molar ratio of carbon dioxide gas and methane is 0.7-1.2, under the condition of cerium oxide catalyst supported by magnesium aluminum spinel, to prepare synthesis gas, and the gas production ratio is about 70-80%.
[0037] (4) Magnesium oxide powder enters the silo and exchanges heat with the air in the jacket in the rotary heat exchanger. The outlet air temperature can reach 375-425°C. It is introduced into...
PUM
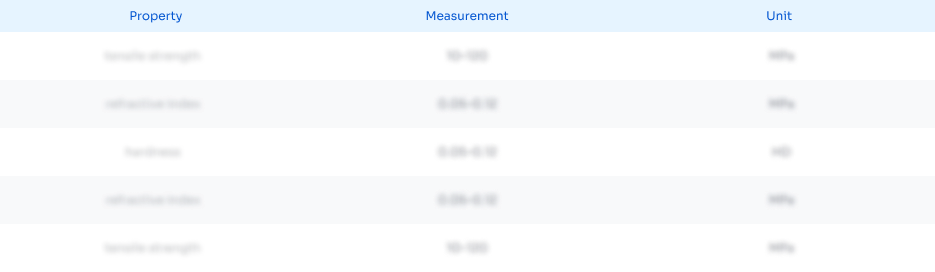
Abstract
Description
Claims
Application Information

- R&D
- Intellectual Property
- Life Sciences
- Materials
- Tech Scout
- Unparalleled Data Quality
- Higher Quality Content
- 60% Fewer Hallucinations
Browse by: Latest US Patents, China's latest patents, Technical Efficacy Thesaurus, Application Domain, Technology Topic, Popular Technical Reports.
© 2025 PatSnap. All rights reserved.Legal|Privacy policy|Modern Slavery Act Transparency Statement|Sitemap|About US| Contact US: help@patsnap.com