A Passive Bending Axial Rotation Mechanism Based on Variable Cross-section Cross Springs
A technology of axial rotation and variable cross-section, applied in the field of passive bending axial rotation mechanism, multi-stage passive bending deformation and axial rotation mechanical mechanism, can solve the problem of passive deformation of bionic fish, etc.
- Summary
- Abstract
- Description
- Claims
- Application Information
AI Technical Summary
Problems solved by technology
Method used
Image
Examples
Embodiment Construction
[0033] Now in conjunction with embodiment, accompanying drawing, the present invention will be further described:
[0034] The overall structure of the embodiment of the present invention is shown in schematic figure 1, with six levels of cross reeds and three axially rotating cross reed units; the mechanism shown in the figure, the cross reeds that undertake the bending task are cross reeds with variable cross-sections, and the two ends are connected to the free ends of the arc surface. An axially rotating cross-reed unit is connected between the two-stage curved cross-reed units, which are distributed according to the order: No. 1 curved cross-reed unit 1 connects to No. 2 curved cross-reed unit 2, and then connects to No. 1 The axially rotating cross reed unit 3 is connected to the No. 3 curved cross reed unit 4 and the No. 4 curved cross reed unit 5 in turn, and then connected to the No. 2 axially rotating cross reed unit 6, and connected to No. 5 in turn The No. 6 curved...
PUM
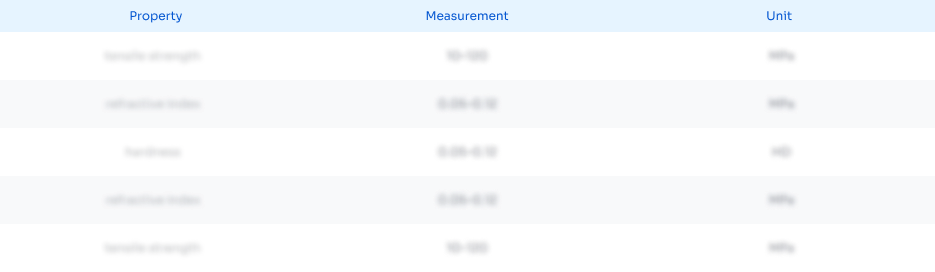
Abstract
Description
Claims
Application Information

- R&D
- Intellectual Property
- Life Sciences
- Materials
- Tech Scout
- Unparalleled Data Quality
- Higher Quality Content
- 60% Fewer Hallucinations
Browse by: Latest US Patents, China's latest patents, Technical Efficacy Thesaurus, Application Domain, Technology Topic, Popular Technical Reports.
© 2025 PatSnap. All rights reserved.Legal|Privacy policy|Modern Slavery Act Transparency Statement|Sitemap|About US| Contact US: help@patsnap.com