Positioning mechanism for disassembling and assembling gear shaft for gear pump
A positioning mechanism and gear pump technology, applied in workpiece clamping devices, hand-held tools, manufacturing tools, etc., can solve problems such as loud noise, lack of positioning mechanism for gear shafts, affecting normal rotation, etc., to improve accuracy, improve The effect of assembly quality
- Summary
- Abstract
- Description
- Claims
- Application Information
AI Technical Summary
Problems solved by technology
Method used
Image
Examples
Embodiment
[0032] as attached figure 1 to attach Figure 9 Shown:
[0033] The present invention provides a positioning mechanism for gear pumps when the gear shaft is folded and assembled, including a base 1; the base 1 is a rectangular plate base structure, and a slideway 2 with a rectangular notch structure is provided in the middle of the plate base, and the slideway In 2, a double-headed reverse lead screw 4 is installed by means of rotation and coordination, which constitutes a screw-type transmission mechanism, and the two-way reverse screw can make the mechanism matched on the two-stage screw rods realize opposite and opposite directions. Synchronous moving action in the direction; the middle position of the slideway 2 is provided with a slide rail 3 structure, and through this slide rail 3 structure, there are two slide seats 5 on the left and right, and the bottoms of the two slide seats 5 are also passed through The circular threaded hole fits on the left and right sections ...
PUM
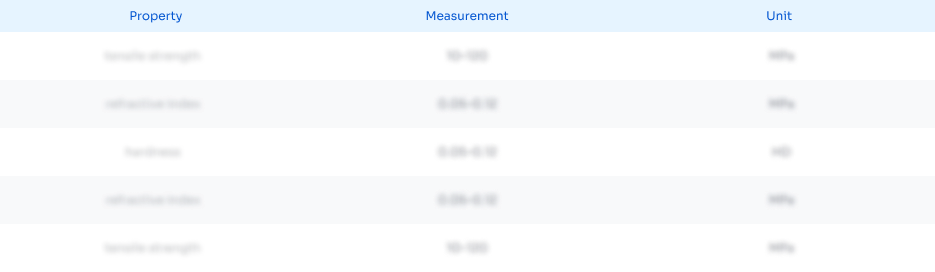
Abstract
Description
Claims
Application Information

- R&D Engineer
- R&D Manager
- IP Professional
- Industry Leading Data Capabilities
- Powerful AI technology
- Patent DNA Extraction
Browse by: Latest US Patents, China's latest patents, Technical Efficacy Thesaurus, Application Domain, Technology Topic, Popular Technical Reports.
© 2024 PatSnap. All rights reserved.Legal|Privacy policy|Modern Slavery Act Transparency Statement|Sitemap|About US| Contact US: help@patsnap.com