Cardanol grafted high-density polyethylene synthesized by reactive extrusion and application thereof in bamboo-plastic composite material
A technology of high-density polyethylene and composite materials, applied in the field of reactive extrusion synthesis of cardanol grafted high-density polyethylene, to achieve the effects of preventing thermal degradation, increasing grafting rate, and low processing temperature
- Summary
- Abstract
- Description
- Claims
- Application Information
AI Technical Summary
Problems solved by technology
Method used
Image
Examples
Embodiment 1
[0019] step one
[0020] After 1g of lauroyl peroxide (LPO) and 1g of dibenzoyl peroxide (BPO) were dissolved in 70g of cardanol, they were added to 1000g of high-density polyethylene (HDPE) resin, stirred at a high speed and mixed evenly, and then extruded with a twin-screw. The extruder (the temperature of the solid conveying section, the melting section, the reaction mixing section, and the melt conveying section of the extruder are respectively 150°C, 160°C, 170°C, and 160°C) is extruded, water-cooled, and granulated to obtain a reactive extruded product. The product cardanol grafted high-density polyethylene (grafting rate 6.82%);
[0021] step two
[0022] After 1000g cardanol grafted high-density polyethylene and 300g bamboo powder are mixed evenly at a high speed, utilize twin-screw extruder (the temperature of extruder solid delivery section, melting section, reaction mixing section and melt delivery section is respectively 150°C, 160°C, 170°C, 160°C) to obtain bamb...
Embodiment 2
[0025] step one
[0026] After 0.1g of lauroyl peroxide (LPO) and 2g of dibenzoyl peroxide (BPO) were dissolved in 150g of cardanol, they were added to 1000g of high-density polyethylene (HDPE) resin. The extruder (the temperature of the extruder solid delivery section, melting section, reaction mixing section, and melt delivery section are 150°C, 160°C, 170°C, and 160°C respectively) is extruded, water-cooled, and granulated to obtain the reaction Extrusion product cardanol grafted high-density polyethylene (grafting rate 4.73%);
[0027] step two
[0028] 1000g of cardanol-grafted high-density polyethylene and 700g of bamboo powder were mixed evenly at high speed, and then hot-pressed at a temperature of 160°C by a hot press to obtain a bamboo-plastic composite material.
Embodiment 3
[0030] step one
[0031] After dissolving 2g of lauroyl peroxide (LPO) and 0.1g of dibenzoyl peroxide (BPO) in 70g of cardanol, add it to 1000g of high-density polyethylene (HDPE) resin, stir and mix evenly at a high speed, and then use a twin-screw The extruder (the temperature of the extruder solid delivery section, melting section, reaction mixing section, and melt delivery section are 140°C, 140°C, 150°C, and 140°C respectively) is extruded, water-cooled, and granulated to obtain the reaction Extrusion product cardanol grafted high-density polyethylene (grafting rate 4.27%);
[0032] step two
[0033] After mixing 1000g of cardanol-grafted high-density polyethylene with 500g of bamboo powder at a high speed, they are extruded using an injection molding machine (the heating temperature is 150°C, 150°C, 160°C, and 170°C from the feed inlet) to obtain bamboo plastic. composite material.
PUM
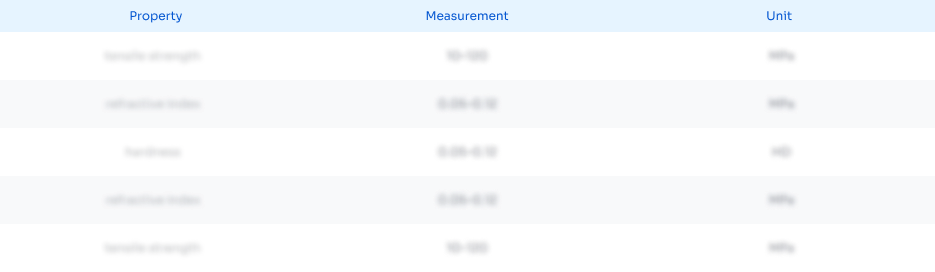
Abstract
Description
Claims
Application Information

- R&D
- Intellectual Property
- Life Sciences
- Materials
- Tech Scout
- Unparalleled Data Quality
- Higher Quality Content
- 60% Fewer Hallucinations
Browse by: Latest US Patents, China's latest patents, Technical Efficacy Thesaurus, Application Domain, Technology Topic, Popular Technical Reports.
© 2025 PatSnap. All rights reserved.Legal|Privacy policy|Modern Slavery Act Transparency Statement|Sitemap|About US| Contact US: help@patsnap.com