Temperature control anti-cracking method for hot cement concrete in lining structure
A cement concrete, temperature control anti-cracking technology, applied in the direction of instruments, calculations, electrical digital data processing, etc., can solve the problems of inability to control temperature control and anti-cracking, no calculation method, etc., to achieve temperature control anti-cracking, good effect, scientific strong effect
- Summary
- Abstract
- Description
- Claims
- Application Information
AI Technical Summary
Problems solved by technology
Method used
Image
Examples
Embodiment 1
[0035] The 1.0m thick (F2 type) lining structure of the Xiluodu flood discharge tunnel is medium hot cement concrete
[0036] Taking the 1.0m thick (F2 type) lining as an example, the finite element method is used for simulation calculation. The calculation conditions are: start pouring on July 1, the pouring temperature is 27°C, no water cooling temperature control measures are taken, and the side wall adopts C 90 40 normal concrete, the top arch adopts C 25 For pumping concrete, only the side walls and the top arch are studied, and the base plate pouring is not considered. The formwork is removed after 3 days of pouring. The interval between side wall and top arch pouring is 31 days, and the length of the joint is 9m.
[0037] The maximum temperature, the maximum internal surface temperature difference and the occurrence time of the typical parts of the 1.0m thick (F2 type) lined concrete side wall are shown in Table 1 below, and the temperature duration curve is shown in ...
Embodiment 2
[0055] The lining structure of the Xiluodu flood discharge tunnel is 0.8m and 1.5m thick with medium-heat cement concrete
[0056] In order to analyze the applicability of formula 1 for lining thickness and water cooling conditions, for image 3 For the section of the lining structure, keep the section size after lining unchanged and only change the thickness of the lining. First, use the finite element method to simulate and calculate, and then use formula 1 to calculate the maximum internal temperature occurrence age d tm Calculation.
[0057] Finite element simulation calculation, the calculation scheme in the case of water cooling is as follows: pouring starts on July 1 in summer, the bottom plate and side and roof arches are poured separately, and the pouring interval is 31 days; the pouring temperature is 18°C, the distance between water pipes is 1.0m, and the water Cool in water at 15°C for 15 days, remove the mold after 3 days, and sprinkle water on the surface for 2...
PUM
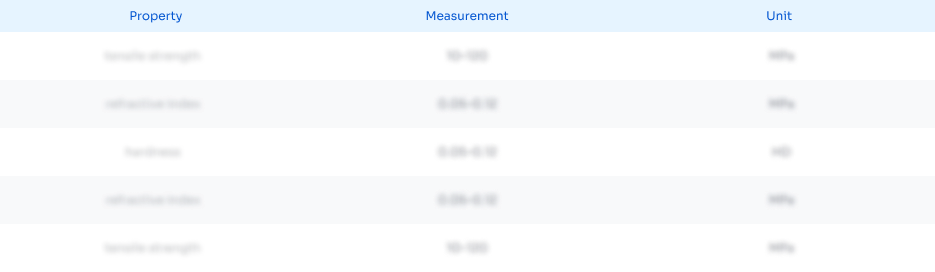
Abstract
Description
Claims
Application Information

- R&D
- Intellectual Property
- Life Sciences
- Materials
- Tech Scout
- Unparalleled Data Quality
- Higher Quality Content
- 60% Fewer Hallucinations
Browse by: Latest US Patents, China's latest patents, Technical Efficacy Thesaurus, Application Domain, Technology Topic, Popular Technical Reports.
© 2025 PatSnap. All rights reserved.Legal|Privacy policy|Modern Slavery Act Transparency Statement|Sitemap|About US| Contact US: help@patsnap.com