Formation and capacity-grading method for lithium battery
A lithium battery and capacity-division technology, applied in secondary batteries, electrochemical generators, secondary battery charging/discharging, etc. The effect of improving the pass rate and electrical performance consistency and improving the pass rate
- Summary
- Abstract
- Description
- Claims
- Application Information
AI Technical Summary
Problems solved by technology
Method used
Examples
Embodiment 1
[0054]The lithium battery is precharged, aged at room temperature, formed, aged at high temperature, K value test, capacity divided and sorted sequentially. The precharge steps are:
[0055] (1) Put the assembled battery on hold for 3 minutes at a temperature of 22-28°C;
[0056] (2) Charge the battery with a constant current of 0.5C for 4 minutes;
[0057] (3) Perform the first OCV test on the battery cell after charging, and the battery voltage range after precharging is required to be 2.0-2.2V.
[0058] For the normal temperature aging, the temperature is 22-28° C., and the aging time is 48 hours.
[0059] Described conversion step is:
[0060] (1) Charge the battery that has been aged at room temperature at a constant current of 0.1C for 120 minutes, and the upper limit of the charging voltage is 3.6V, and put the battery on hold for 8 minutes;
[0061] (2) Charge the charged battery with a constant current at 0.5C for 105 minutes, the upper limit of the charging voltag...
Embodiment 2
[0076] The lithium battery is precharged, aged at room temperature, formed, aged at high temperature, K value test, capacity divided and sorted sequentially. The precharge steps are:
[0077] (1) Put the assembled battery on hold for 5 minutes at a temperature of 22-28°C;
[0078] (2) Charge the battery with a constant current of 0.3C for 10 minutes;
[0079] (3) Perform the first OCV test on the battery cell after charging, and the battery voltage range after pre-charging is required to be 2.2-2.5V.
[0080] For the normal temperature aging, the temperature is 22-28° C., and the aging time is 24 hours.
[0081] Described conversion step is:
[0082] (1) Charge the battery that has been aged at room temperature at a constant current of 0.2C for 60 minutes, and the upper limit of the charging voltage is 3.6V, and put the battery on hold for 5 minutes;
[0083] (2) Charge the charged battery with a constant current at 0.33C for 160 minutes, and the upper limit of the charging...
Embodiment 3
[0098] The lithium battery is precharged, aged at room temperature, formed, aged at high temperature, K value test, capacity divided and sorted sequentially. The precharge steps are:
[0099] (1) Put the assembled battery on hold for 4 minutes at a temperature of 22-28°C;
[0100] (2) Charge the battery at a constant current of 0.8C for 2 minutes;
[0101] (3) Perform the first OCV test on the battery cell after charging, and the battery voltage range after pre-charging is required to be 1.8-2.0V.
[0102] For the normal temperature aging, the temperature is 22-28° C., and the aging time is 72 hours.
[0103] Described conversion step is:
[0104] (1) Charge the battery that has been aged at room temperature at a constant current of 0.3C for 50 minutes, and the upper limit of the charging voltage is 3.7V, and put the battery on hold for 10 minutes;
[0105] (2) Charge the charged battery with a constant current at 0.6C for 90 minutes, and the upper limit of the charging vol...
PUM
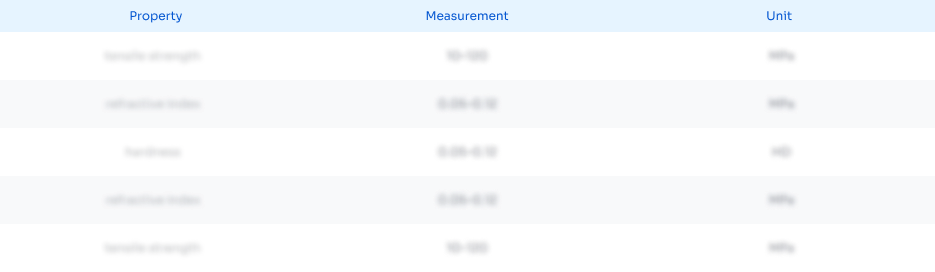
Abstract
Description
Claims
Application Information

- R&D
- Intellectual Property
- Life Sciences
- Materials
- Tech Scout
- Unparalleled Data Quality
- Higher Quality Content
- 60% Fewer Hallucinations
Browse by: Latest US Patents, China's latest patents, Technical Efficacy Thesaurus, Application Domain, Technology Topic, Popular Technical Reports.
© 2025 PatSnap. All rights reserved.Legal|Privacy policy|Modern Slavery Act Transparency Statement|Sitemap|About US| Contact US: help@patsnap.com