Bionic flexible morphing wing
A wing and flexible technology, applied in the field of deformable UAV structure, can solve the problems of energy waste, environmental pollution, reduce the service life of the aircraft, increase the flight resistance of the aircraft, and achieve the reduction of maintenance difficulty and cost, aerodynamics Excellent performance, reduced drag and noise
- Summary
- Abstract
- Description
- Claims
- Application Information
AI Technical Summary
Problems solved by technology
Method used
Image
Examples
Embodiment Construction
[0038] see figure 1 , figure 2 , image 3 , Figure 4 , Figure 5 and Figure 6 As shown, the present invention includes a first transverse framework 1, a second transverse framework 2, a third transverse framework 3, a fourth transverse framework 4, a group A longitudinal framework 5, a B group longitudinal framework 6, a heat insulating layer 7, and a wing covering Skin 8, connecting device 9, fixing device 10, group A temperature control system 11, group B temperature control system 12;
[0039] The first transverse framework 1, the second transverse framework 2, the third transverse framework 3 and the fourth transverse framework 4 are distributed at intervals from the inside to the outside, the longitudinal frameworks 5 of group A and the longitudinal frameworks 6 of group B are distributed at intervals, the longitudinal frameworks of group A 5 and Group B’s longitudinal skeletons 6 all fit together through the first transverse skeleton 1, the second transverse skel...
PUM
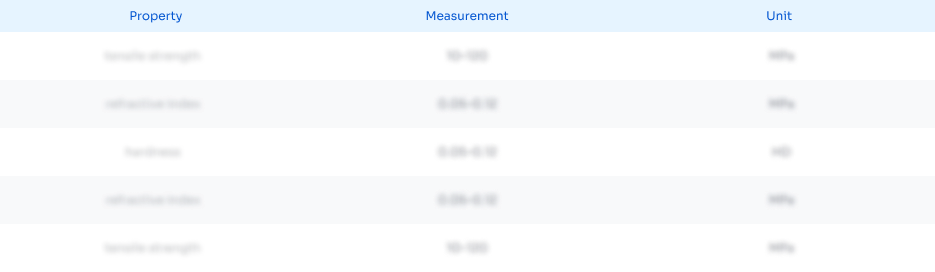
Abstract
Description
Claims
Application Information

- R&D
- Intellectual Property
- Life Sciences
- Materials
- Tech Scout
- Unparalleled Data Quality
- Higher Quality Content
- 60% Fewer Hallucinations
Browse by: Latest US Patents, China's latest patents, Technical Efficacy Thesaurus, Application Domain, Technology Topic, Popular Technical Reports.
© 2025 PatSnap. All rights reserved.Legal|Privacy policy|Modern Slavery Act Transparency Statement|Sitemap|About US| Contact US: help@patsnap.com