Method for recycling calcium-rich pyrochlore from weathered high-mud carbonate type niobium polymetallic ore
A carbonate type, polymetallic ore technology, applied in chemical instruments and methods, wet separation, solid separation, etc., can solve the problem of lack of separation process of calcium-rich pyrochlore, unrecoverable pyrochlore, and recovery rate. low problems, to achieve the effect of high grade, high recovery rate and strong adaptability
- Summary
- Abstract
- Description
- Claims
- Application Information
AI Technical Summary
Problems solved by technology
Method used
Image
Examples
Embodiment 1
[0031] A method for recovering calcium-rich pyrochlore from weathered high-mud carbonate-type niobium polymetallic ore, comprising the steps of:
[0032] S1. Raw ore grinding to -0.5mm accounts for 92%;
[0033] S2. Add water to the product after grinding to adjust the pulp concentration to 25%, stir and scrub for 10 minutes, and carry out spiral gravity separation in the spiral chute to obtain coarse concentrate and spiral tailings;
[0034] S3. Regrind the coarse concentrate to -0.074mm to account for 70%, add water to adjust the slurry to a pulp concentration of 30%, add floating phosphorus reagents, and perform apatite flotation to obtain phosphorus concentrate and floating phosphorus tailings;
[0035] S4. Concentrate the floating phosphorus tailings to a slurry concentration of 30%, add floating niobium reagents to the floating phosphorus tailings, and perform niobium flotation, niobium concentrate and floating niobium tailings.
[0036] See Table 1 for the phosphorus f...
Embodiment 2
[0038] A method for recovering calcium-rich pyrochlore from weathered high-mud carbonate-type niobium polymetallic ore, comprising the steps of:
[0039] S1. Raw ore grinding to -0.5mm accounts for 96%;
[0040] S2. Add water to the ground product to adjust the pulp concentration to 35%, stir and scrub for 8 minutes, and perform spiral gravity separation in the spiral chute to obtain coarse concentrate and spiral tailings;
[0041] S3. Regrind the coarse concentrate to -0.074mm to account for 85%, add water to adjust the slurry to a pulp concentration of 25%, add floating phosphorus reagents, and perform apatite flotation to obtain phosphorus concentrate and floating phosphorus tailings;
[0042] S4. Concentrate the floating phosphorus tailings to a pulp concentration of 35%, add floating niobium reagents to the floating phosphorus tailings, and perform niobium flotation, niobium concentrate and floating niobium tailings.
[0043] See Table 1 for the phosphorus flotation agen...
Embodiment 3
[0045] A method for recovering calcium-rich pyrochlore from weathered high-mud carbonate-type niobium polymetallic ore, comprising the steps of:
[0046] S1. Raw ore grinding to -0.5mm accounts for 90%;
[0047] S2. Add water to the product after grinding to adjust the pulp concentration to 20%, stir and scrub for 5 minutes, and carry out spiral gravity separation in the spiral chute to obtain coarse concentrate and spiral tailings;
[0048] S3. Regrind the coarse concentrate to -0.074mm to account for 55%, add water to adjust the slurry to a pulp concentration of 35%, add floating phosphorus reagents, and perform apatite flotation to obtain phosphorus concentrate and floating phosphorus tailings;
[0049] S4. Concentrate the floating phosphorus tailings to a slurry concentration of 25%, add floating niobium reagents to the floating phosphorus tailings, and perform niobium flotation, niobium concentrate and floating niobium tailings.
[0050] See Table 1 for the phosphorus fl...
PUM
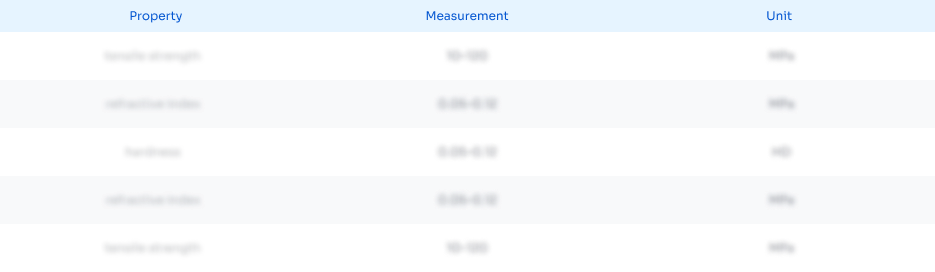
Abstract
Description
Claims
Application Information

- R&D
- Intellectual Property
- Life Sciences
- Materials
- Tech Scout
- Unparalleled Data Quality
- Higher Quality Content
- 60% Fewer Hallucinations
Browse by: Latest US Patents, China's latest patents, Technical Efficacy Thesaurus, Application Domain, Technology Topic, Popular Technical Reports.
© 2025 PatSnap. All rights reserved.Legal|Privacy policy|Modern Slavery Act Transparency Statement|Sitemap|About US| Contact US: help@patsnap.com