A model-free tracking control method and medium for a piezoelectric ceramic actuator
A piezoelectric ceramic and tracking control technology, which is applied in the field of servo control to achieve good tracking accuracy, wide dynamic response range, and accurate phase tracking
- Summary
- Abstract
- Description
- Claims
- Application Information
AI Technical Summary
Problems solved by technology
Method used
Image
Examples
Embodiment 1
[0051] A method for model-free tracking control of a piezoelectric ceramic actuator, comprising the steps of:
[0052] S1, based on the cumulant c(t) of the rotational speed pulse signal of the rotor of the external flywheel or the control torque gyroscope, the rotational speed frequency f of the rotor at any time t in the process of variable speed or steady speed is obtained by the method of least squares; then according to the obtained Describe the dynamic and static unbalance of the bearing structure and the rotor in the rotor, and estimate the micro-vibration frequency component f at any time i ;
[0053] S2, based on the displacement reference control signal x(t), the micro-vibration frequency component f described in S1 i , using the robust regression method to estimate the effect of the displacement reference control signal x(t) on the micro-vibration frequency component f i The coefficients of the linear representation of the sine-cosine basis functions of
[0054...
Embodiment 2
[0059] A computer-readable storage medium, on which a computer program is stored. When the program is executed by a processor, the steps of the method described in Embodiment 1 are implemented.
Embodiment 3
[0061] The invention provides a model-free tracking control method for piezoelectric ceramic actuators, such as figure 1 As shown in the block diagram of the control system in the present invention, it includes the following links:
[0062] (1) PI preliminary tracking control
[0063] PID control has prominent advantages such as good object adaptability and parameter robustness. In view of the nonlinear characteristics of piezoelectric ceramic actuators such as hysteresis and creep, and their long-term exposure to harsh space environment tests such as radiation, resulting in their performance degrading over time, and the specific characteristics of different individuals are different, the use of PID Preliminary displacement tracking control, and when the PID parameters are adjusted properly, the stability and robustness of the control system can be guaranteed without the piezoelectric ceramic actuator model, and the piezoelectric ceramic actuator can be controlled to a certai...
PUM
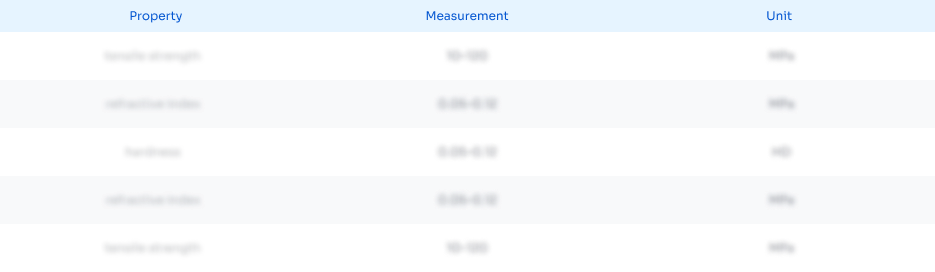
Abstract
Description
Claims
Application Information

- R&D
- Intellectual Property
- Life Sciences
- Materials
- Tech Scout
- Unparalleled Data Quality
- Higher Quality Content
- 60% Fewer Hallucinations
Browse by: Latest US Patents, China's latest patents, Technical Efficacy Thesaurus, Application Domain, Technology Topic, Popular Technical Reports.
© 2025 PatSnap. All rights reserved.Legal|Privacy policy|Modern Slavery Act Transparency Statement|Sitemap|About US| Contact US: help@patsnap.com