Production process for high-precision bearing roller for rail transit
A technology for bearing rollers and rail transportation, applied in the field of bearing roller processing, to achieve long-term stable operation, ensure consistency, and stable force
- Summary
- Abstract
- Description
- Claims
- Application Information
AI Technical Summary
Problems solved by technology
Method used
Image
Examples
Embodiment Construction
[0041] Refer to attached figure 1 , the specific steps of the production process of high-precision bearing rollers for rail transit:
[0042] 1. Cold heading: use a four-station high-speed cold heading machine to draw the steel and press it into a roller blank.
[0043] , Heat treatment: Heat treatment is to complete the quenching and tempering treatment of the cold heading roller blank in the solid range through certain heating, heat preservation and cooling, cleaning assistance, etc. to change its structure and performance, and to obtain product characteristic requirements. A key process. The heat treatment of the project is a fully automatic mesh belt furnace heat treatment production line.
[0044] , Hard grinding 1: Grinding the outer diameter of the roller, removing part of the grinding amount, so that the raceway surface of the roller meets the process size requirements, laying the foundation for the geometric accuracy of the subsequent hard grinding 2 and hard grindi...
PUM
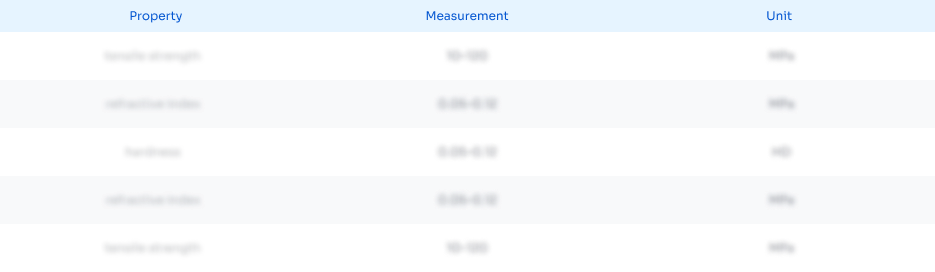
Abstract
Description
Claims
Application Information

- R&D
- Intellectual Property
- Life Sciences
- Materials
- Tech Scout
- Unparalleled Data Quality
- Higher Quality Content
- 60% Fewer Hallucinations
Browse by: Latest US Patents, China's latest patents, Technical Efficacy Thesaurus, Application Domain, Technology Topic, Popular Technical Reports.
© 2025 PatSnap. All rights reserved.Legal|Privacy policy|Modern Slavery Act Transparency Statement|Sitemap|About US| Contact US: help@patsnap.com