A low-temperature rapid demulsifier for polymer flooding crude oil and its preparation method
A crude oil demulsifier and demulsifier technology, applied in the direction of chemical dehydration/demulsification, etc., can solve the problems of high oil content in the extracted water, unsatisfactory demulsification effect, and thick emulsification layer, and achieve low oil content in the extracted water. Excellent compatibility and synergy, clear oil-water interface
- Summary
- Abstract
- Description
- Claims
- Application Information
AI Technical Summary
Problems solved by technology
Method used
Image
Examples
Embodiment 1
[0040] 1. Phenolic resin synthesis
[0041] According to the molar ratio, phenol: aldehyde = 1.5: 2.6, successively put octylphenol and benzaldehyde into the reactor, then add 25% xylene of the total mass of octylphenol and benzaldehyde, stir and heat up to 35-45°C , mixed for 1 hour, added 0.25% sulfuric acid of the total mass of octylphenol and benzaldehyde, raised the temperature to 110-120°C and refluxed for 1 hour, gradually heated to 130-135°C and refluxed for 3 hours, cooled to room temperature to obtain phenolic resin R1.2 .Modification of phenolic resin
[0042] According to the molar ratio, phenolic resin R1: epichlorohydrin: hexadecylamine=0.8: 3: 1, first add the phenolic resin R1 in step 1 to the reactor, then add the mass percentage concentration of 3% of the phenolic resin quality It is 60% potassium hydroxide deionized aqueous solution, stir evenly, heat to 90-105°C, then slowly add a proportioned amount of epichlorohydrin to the phenolic resin, keep it warm f...
Embodiment 2
[0050] 1. Phenolic resin synthesis
[0051] According to the molar ratio, phenol: aldehyde = 1.3: 2.1, sequentially put naphthol and furfural into the reactor, then add 22% xylene of the total mass of naphthol and furfural, stir and heat up to 35-45°C, and mix for 1 hour , adding 0.21% benzenesulfonic acid based on the total mass of naphthol and furfural, raising the temperature to 110-120° C. for reflux for 1 hour, gradually heating to 130-135° C. for reflux for 3 hours, cooling to normal temperature to obtain phenolic resin R2.
[0052] 2. Modification of phenolic resin
[0053] According to the molar ratio, phenolic resin R2: epoxy chlorobutane: octadecylamine=0.8: 3: 1, the phenolic resin R1 in the step 1 is added in the reactor earlier, then add the quality of 3% of the phenolic resin quality The percentage concentration is 58% sodium hydroxide deionized aqueous solution, stir evenly, heat to 90 ~ 105 ℃, then slowly add the proportional amount of epoxy chlorobutane to th...
Embodiment 3
[0061] 1. Phenolic resin synthesis
[0062] According to the molar ratio, phenol: aldehyde = 1.2: 2.3, p-tert-butylphenol and formaldehyde are dropped into the reactor successively, then add 24% xylene of the total mass of p-tert-butylphenol and formaldehyde, stir and heat up to 35 ~ 45°C, mix for 1 hour, add 0.25% petroleum sulfonic acid based on the total mass of p-tert-butylphenol and formaldehyde, heat up to 110-120°C and reflux for 1 hour, gradually heat to 130-135°C and reflux for 3 hours, cool to room temperature to obtain Phenolic resin R3.
[0063] 2. Modification of phenolic resin
[0064] According to the molar ratio, phenolic resin R3: epichlorohydrin: methyldiethanolamine=0.8: 3: 1, first add the phenolic resin R1 in step 1 to the reactor, then add the mass percentage of 3% of the phenolic resin quality Concentration of 60% potassium hydroxide deionized aqueous solution, stir evenly, heat to 90 ~ 105 ℃, then slowly add a proportioned amount of epichlorohydrin to...
PUM
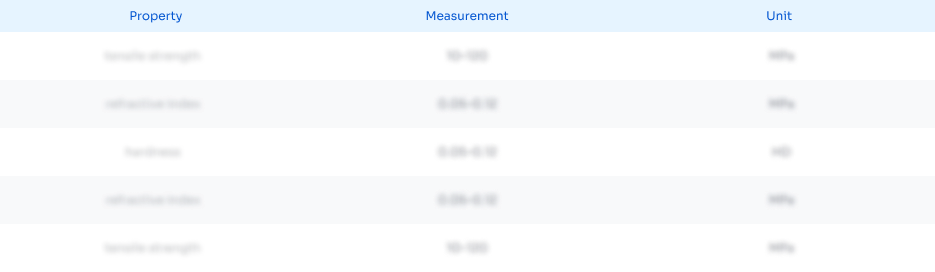
Abstract
Description
Claims
Application Information

- R&D
- Intellectual Property
- Life Sciences
- Materials
- Tech Scout
- Unparalleled Data Quality
- Higher Quality Content
- 60% Fewer Hallucinations
Browse by: Latest US Patents, China's latest patents, Technical Efficacy Thesaurus, Application Domain, Technology Topic, Popular Technical Reports.
© 2025 PatSnap. All rights reserved.Legal|Privacy policy|Modern Slavery Act Transparency Statement|Sitemap|About US| Contact US: help@patsnap.com