Hydraulic quick linkage clamping mechanism
A clamping mechanism and fast technology, applied in the direction of metal processing equipment, grinding workpiece support, manufacturing tools, etc., can solve the problems that affect the accuracy of workpiece use, high use cost, and low work efficiency, so as to improve work efficiency and manufacture Low cost and long service life
- Summary
- Abstract
- Description
- Claims
- Application Information
AI Technical Summary
Problems solved by technology
Method used
Image
Examples
Embodiment 1
[0024] like Figure 1-6 As shown, a hydraulic fast linkage clamping mechanism includes a base 1, a clamp body 2 and an ash removal sleeve 17, the clamp body 2 is welded on the top side of the base 1, and a piston groove 3 is opened at the top end of the clamp body 2, The piston rod 4 is inserted in the piston groove 3, the liquid material pipe 5 is installed on one side of the piston groove 3 through the pipe groove, the piston groove 3 is connected with the liquid material pipe 5, and the inner bottom of the clamp body 2 is inserted Elastic deformation sleeve 6 is installed in the groove, elastic clamping sleeve 7 is inserted in the elastic deformation sleeve 6, workpiece 8 is inserted in the elastic clamping sleeve 7, one end of the liquid material pipe 5 is connected with the elastic deformation sleeve 6 in turn, The liquid material pipe 5 is filled with liquid plastic 14, the bottom of the elastic deformation sleeve 6 is inserted with a limit block 11, and the limit block ...
Embodiment 2
[0035] like Figure 1-6 As shown, a hydraulic fast linkage clamping mechanism includes a base 1, a clamp body 2 and a grinding sleeve, the clamp body 2 is welded on the top side of the base 1, and a piston groove 3 is opened at the top end of the clamp body 2. A piston rod 4 is inserted in the piston groove 3, and a liquid material pipe 5 is installed through a pipe groove on one side of the piston groove 3, and the piston groove 3 is connected through the liquid material pipe 5, and the inner bottom of the clamp body 2 is installed through a slot An elastic deformation sleeve 6, an elastic clamping sleeve 7 is inserted in the elastic deformation sleeve 6, a workpiece 8 is inserted in the elastic clamping sleeve 7, one end of the liquid material pipe 5 is connected with the elastic deformation sleeve 6 in sequence, and the The liquid material pipe 5 is filled with liquid plastic 14, the bottom of the elastic deformation sleeve 6 is inserted with a limit block 11, the limit blo...
PUM
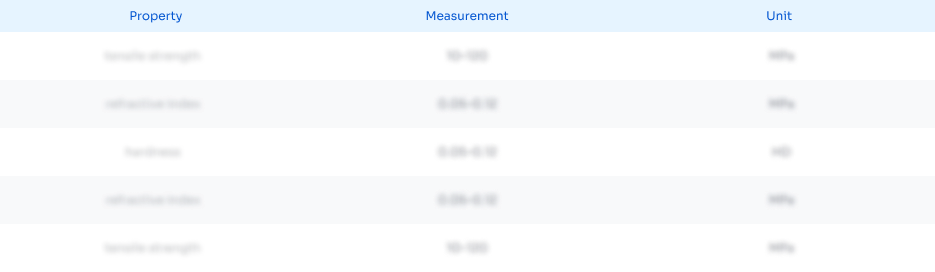
Abstract
Description
Claims
Application Information

- R&D
- Intellectual Property
- Life Sciences
- Materials
- Tech Scout
- Unparalleled Data Quality
- Higher Quality Content
- 60% Fewer Hallucinations
Browse by: Latest US Patents, China's latest patents, Technical Efficacy Thesaurus, Application Domain, Technology Topic, Popular Technical Reports.
© 2025 PatSnap. All rights reserved.Legal|Privacy policy|Modern Slavery Act Transparency Statement|Sitemap|About US| Contact US: help@patsnap.com