Crystalline CFRTP forming machining method
A forming processing and crystallization technology, which is applied in the field of forming processing of crystalline CFRTP, can solve the problems affecting the mechanical properties of CFRTP and weakening the fiber reinforcement in the resin, so as to avoid the problem of fiber bundle flow and improve the mechanical properties.
- Summary
- Abstract
- Description
- Claims
- Application Information
AI Technical Summary
Problems solved by technology
Method used
Image
Examples
Embodiment 1
[0041] This embodiment provides a forming and processing method for crystalline CFRTP. Since polyamide 6 is a crystalline polymer commonly used as a resin matrix for thermoplastic fiber-reinforced composite materials, this embodiment uses carbon fiber / polyamide 6 composite The board is the raw material for processing, and its DSC curve is as follows figure 1 As shown, it specifically includes the following steps:
[0042] Step (1) First, quench the carbon fiber / polyamide 6 composite board: heat the prepared carbon fiber / polyamide 6 composite board to 250°C and keep it warm for 15 minutes until the resin is completely melted, then quickly heat the carbon fiber / polyamide 6 composite board Put it between two normal temperature steel plates for rapid cooling. Through the rapid cooling of polyamide 6, the crystallization of polyamide 6 crystals is in different stages, thereby widening the melting range.
[0043] Step (2) Heating and deformation: After step (1), heat the carbon fi...
Embodiment 2
[0046] This embodiment provides a forming and processing method for crystalline CFRTP. Since polyamide 6 is a crystalline polymer commonly used as a resin matrix for thermoplastic fiber-reinforced composite materials, this embodiment uses carbon fiber / polyamide 6 composite The board is the raw material for processing, and the specific implementation includes the following steps:
[0047] Step (1) First, quench the carbon fiber / polyamide 6 composite board: heat the prepared carbon fiber / polyamide 6 composite board to 245°C and keep it warm for 20 minutes until the resin is completely melted, then quickly heat the carbon fiber / polyamide 6 composite board Quickly cool in coolant.
[0048] Step (2) Heating and deformation: After step (1), put the carbon fiber / polyamide 6 composite board and the mold into a vacuum bag, and seal the vacuum bag. Heat the vacuum bag as a whole at a heating rate of 5°C / min. When the temperature reaches 200°C, start to evacuate the vacuum bag and heat ...
Embodiment 3
[0051] This embodiment provides a forming and processing method for crystalline CFRTP. Since polyamide 6 is a crystalline polymer commonly used as a resin matrix for thermoplastic fiber-reinforced composite materials, this embodiment uses carbon fiber / polyamide 6 composite The board is the raw material for processing, and the specific implementation includes the following steps:
[0052] Step (1) First, quench the carbon fiber / polyamide 6 composite board: heat the prepared carbon fiber / polyamide 6 composite board to 250°C and keep it warm for 10 minutes until the resin is completely melted, then quickly heat the carbon fiber / polyamide 6 composite board Quickly cool in coolant.
[0053] Step (2) Heating and deformation: After step (1), put the carbon fiber / polyamide 6 composite board and the mold into a vacuum bag, and seal the vacuum bag. Heat the vacuum bag as a whole at a heating rate of 5°C / min. When the temperature reaches 200°C, start to evacuate the vacuum bag and heat ...
PUM
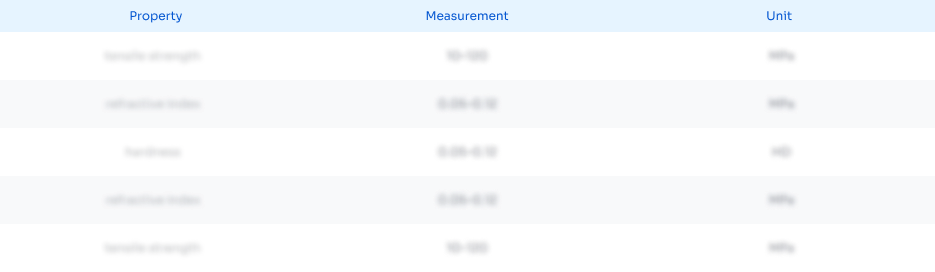
Abstract
Description
Claims
Application Information

- Generate Ideas
- Intellectual Property
- Life Sciences
- Materials
- Tech Scout
- Unparalleled Data Quality
- Higher Quality Content
- 60% Fewer Hallucinations
Browse by: Latest US Patents, China's latest patents, Technical Efficacy Thesaurus, Application Domain, Technology Topic, Popular Technical Reports.
© 2025 PatSnap. All rights reserved.Legal|Privacy policy|Modern Slavery Act Transparency Statement|Sitemap|About US| Contact US: help@patsnap.com