Metallurgical apparatus
The technology of metallurgical equipment and mixing box, which is applied in the field of metallurgical processing, can solve the problems of heavy workload of operators, inconvenient dumping of raw materials, low work efficiency, etc., and achieves the effects of convenient operation, simple structure and improved feeding speed.
- Summary
- Abstract
- Description
- Claims
- Application Information
AI Technical Summary
Problems solved by technology
Method used
Image
Examples
Embodiment 1
[0023] The rotation of the fifth pulley 6116 is controlled by the driving motor 6111, and the fourth pulley 6117 is driven by the first transmission belt 6118 on the fifth pulley 6116 to rotate. The pulley 6113 rotates, and the fourth pulley 6117 drives the driving gear 6442 and the second bevel gear 6441 at the bottom of the fifth rotating shaft 644 to rotate. At the same time, the second transmission belt 6115 on the third pulley 6113 drives the sixth pulley 6114 At the same time, the third pulley 6113 drives the first ratchet part 632 on the first disc 631 to slide and fit with the inner teeth in the first inner ratchet disc 63, so that the first inner ratchet disc 63 and the first inner ratchet disc 63 The first screw rod 82 is in a static state. At this time, due to the rotation of the sixth pulley 6114, the second rotating shaft 711 and the seventh pulley 712 at the top of the second rotating shaft 711 are driven to rotate. At this time, the seventh pulley 712 The third ...
Embodiment 2
[0025] The fifth pulley 6116 is controlled to rotate in reverse by the driving motor 6111, and then the first transmission belt 6118 on the fifth pulley 6116 drives the fourth pulley 6117 to rotate in reverse. At this time, the fourth pulley 6117 drives the first The third pulley 6113 at the top of the rotating shaft 6112 rotates in reverse, and the fourth pulley 6117 drives the driving gear 6442 and the second bevel gear 6441 at the bottom of the fifth rotating shaft 644 to rotate in reverse. The second transmission belt 6115 drives the sixth pulley 6114 to rotate in reverse, and at the same time, the third pulley 6113 drives the first disc 631 to rotate in reverse, so that the first ratchet 632 on the first disc 631 is aligned with the first inner The ratchet disc 63 works together, and then the first inner ratchet disc 63 drives the first screw rod 82 to rotate. The rotation of the screw rod 82 makes the material transfer to the discharge port 83 to realize the automatic co...
PUM
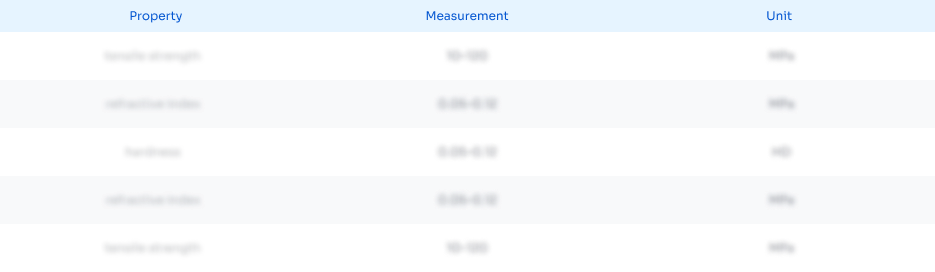
Abstract
Description
Claims
Application Information

- R&D
- Intellectual Property
- Life Sciences
- Materials
- Tech Scout
- Unparalleled Data Quality
- Higher Quality Content
- 60% Fewer Hallucinations
Browse by: Latest US Patents, China's latest patents, Technical Efficacy Thesaurus, Application Domain, Technology Topic, Popular Technical Reports.
© 2025 PatSnap. All rights reserved.Legal|Privacy policy|Modern Slavery Act Transparency Statement|Sitemap|About US| Contact US: help@patsnap.com