Whole working condition composite-structure sliding bearing
A technology of sliding bearings and composite structures, applied to bearing components, shafts and bearings, mechanical equipment, etc., can solve problems such as increased heat generation and easy failure of oil film, and achieve high load-carrying capacity, low friction coefficient, and strong wear resistance Effect
- Summary
- Abstract
- Description
- Claims
- Application Information
AI Technical Summary
Problems solved by technology
Method used
Image
Examples
Embodiment 1
[0026] like figure 1 and figure 2 As shown, this embodiment provides a sliding bearing with composite structure under all working conditions, including a sliding bearing 1, a triple composite texture is provided on the sliding surface of the sliding bearing 1, the triple composite texture includes a plurality of dimple groups, and a plurality of The set of dimples is evenly arranged on the sliding surface 100 of the sliding bearing 1 .
[0027] Each dimple group includes a first dimple 101 , a second dimple 102 and a third dimple 103 . The proportion of the first dimple 101 , the second dimple 102 and the third dimple 103 on the sliding surface 100 of the sliding bearing 1 is in the range of 1-30%.
[0028] The maximum dimension of each first pit 101 in the axial direction is 1-50 microns, and the maximum dimension in the radial direction is 2-5 microns. The maximum dimension of each second pit 102 in the axial direction is 50-100 microns, and the maximum dimension in the ...
Embodiment 2
[0033] like image 3 and Figure 4 As shown, this embodiment provides a sliding bearing with composite structure under all working conditions, including a sliding bearing 1, a triple composite texture is provided on the sliding surface of the sliding bearing 1, the triple composite texture includes a plurality of dimple groups, and a plurality of The set of dimples is evenly arranged on the sliding surface 100 of the sliding bearing 1 .
[0034] Each dimple group includes a first dimple 101 , a second dimple 102 and a third dimple 103 . The proportion of the first dimple 101 , the second dimple 102 and the third dimple 103 on the sliding surface 100 of the sliding bearing 1 is in the range of 1-30%.
[0035] The maximum dimension of each first pit 101 in the axial direction is 1-50 microns, and the maximum dimension in the radial direction is 2-5 microns. The maximum dimension of each second pit 102 in the axial direction is 50-100 microns, and the maximum dimension in the ...
PUM
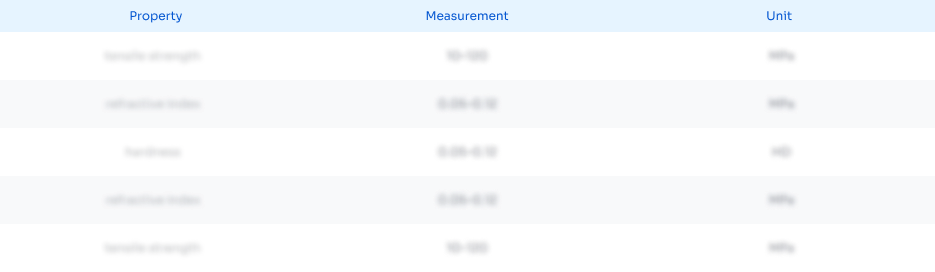
Abstract
Description
Claims
Application Information

- R&D
- Intellectual Property
- Life Sciences
- Materials
- Tech Scout
- Unparalleled Data Quality
- Higher Quality Content
- 60% Fewer Hallucinations
Browse by: Latest US Patents, China's latest patents, Technical Efficacy Thesaurus, Application Domain, Technology Topic, Popular Technical Reports.
© 2025 PatSnap. All rights reserved.Legal|Privacy policy|Modern Slavery Act Transparency Statement|Sitemap|About US| Contact US: help@patsnap.com