Hot working production process of bearing steel tube
A bearing steel pipe and production process technology, which is applied in the field of thermal processing of bearing steel pipes, can solve the problems of easy oxidation of the surface, carbon and decarburization of the surface area of parts, and achieve the effect of strengthening chemical dissolution and accelerating dissolution
- Summary
- Abstract
- Description
- Claims
- Application Information
AI Technical Summary
Problems solved by technology
Method used
Image
Examples
Embodiment Construction
[0017] In order to make the object, technical solution and advantages of the present invention clearer, the present invention will be further described in detail below in conjunction with the accompanying drawings and embodiments. It should be understood that the specific embodiments described here are only used to explain the present invention, not to limit the present invention.
[0018] see figure 1 , the present invention provides a technical solution: a thermal processing production process of bearing steel pipes, including step 1: preparation of a centrifugal billet, alloy melting and pouring in a mold, and making a rough steel pipe billet; step 2: pretreatment of the pipe billet, removing rough The slag layer on the surface of the billet, and ultrasonic cleaning of the tube billet; Step 3: cross-rolling process, using two piercing-rolling and sizing processes, the first piercing-rolling and sizing adopts a smaller deformation ratio, and the second piercing-rolling and s...
PUM
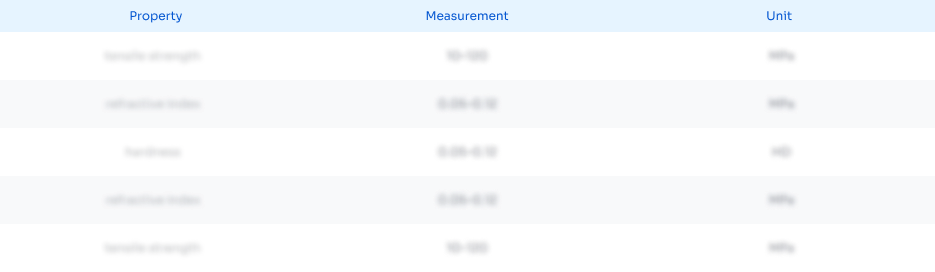
Abstract
Description
Claims
Application Information

- R&D Engineer
- R&D Manager
- IP Professional
- Industry Leading Data Capabilities
- Powerful AI technology
- Patent DNA Extraction
Browse by: Latest US Patents, China's latest patents, Technical Efficacy Thesaurus, Application Domain, Technology Topic, Popular Technical Reports.
© 2024 PatSnap. All rights reserved.Legal|Privacy policy|Modern Slavery Act Transparency Statement|Sitemap|About US| Contact US: help@patsnap.com