Spinel glass ceramic and preparation method thereof
A glass-ceramic and spinel technology, applied in glass manufacturing equipment, glass furnace equipment, manufacturing tools, etc., can solve the problems of long production time, high cost, low efficiency, etc., and achieve short production time and good heat resistance. , the effect of high efficiency
- Summary
- Abstract
- Description
- Claims
- Application Information
AI Technical Summary
Problems solved by technology
Method used
Examples
Embodiment 1
[0025] A spinel glass-ceramic consisting of the following raw materials:
[0026] Basic composition, including the following components in molar percentages: ZnO 20%, Al 2 o 3 22%, SiO 2 43%, ZrO 2 3%, TiO 2 8% and MgO 4%;
[0027] Colorants, which are chromium-containing oxides (Cr 2 o 3 ), the molar percentage of chromium in the basic composition is 0.2%;
[0028] Tin-containing oxides as SnO and / or SnO 2 , the molar percentage of tin in the base composition is 0.1%.
[0029] The preparation method of above-mentioned spinel glass ceramics, comprises the following steps:
[0030] (1) Ingredients: weigh each raw material according to the formula, mix evenly, and obtain the ingredients;
[0031] (2) Melting: melt the batch material at 1600°C for 2 hours;
[0032] (3) Molding and annealing: the smelted molten glass is poured into a mold and then annealed at 620°C;
[0033] (4) Heat treatment: the annealed product is first heat-treated at 780° C. for 2 hours, and t...
Embodiment 2
[0036] A spinel glass-ceramic consisting of the following raw materials:
[0037] Basic composition, including the following components in molar percentages: ZnO 10%, Al 2 o 3 28%, SiO 2 45%, TiO 2 9% and MgO 8%;
[0038] Colorants, manganese-containing oxides (MnO 2 and / or Mn 2 o 3 ), the molar percentage of manganese accounting for basic components is 3%;
[0039] Flux, Na 2 O and K 2 O is a mixture of 1:1 by molar ratio, and the flux accounts for 1% by mole of the base component;
[0040] Tin-containing oxides as SnO and / or SnO 2 , the mole percentage of tin in the base composition is 1%.
[0041] The preparation method of above-mentioned spinel glass ceramics, comprises the following steps:
[0042] (1) Ingredients: weigh each raw material according to the formula, mix evenly, and obtain the ingredients;
[0043] (2) Melting: melting the batch material at 1620°C for 6 hours;
[0044] (3) Molding and annealing: pour the smelted molten glass into a mold, and ...
Embodiment 3
[0048] A spinel glass-ceramic consisting of the following raw materials:
[0049] Basic composition, including the following components in molar percentages: ZnO 16%, Al 2 o 3 16%, SiO 2 55%, TiO 2 9% and MgO 4%;
[0050] Colorants, which are nickel-containing oxides (NiO 2 and / or Ni 2 o 3 ), the molar percentage of nickel in the base composition is 0.2%;
[0051] Flux, Na 2 O and K 2 O is the mixture that is mixed at 1:2 by molar ratio, and the molar percentage that flux accounts for basic component is 2%;
[0052] Tin-containing oxides as SnO and / or SnO 2 , the molar percentage of tin in the base composition is 0.4%.
[0053] The preparation method of above-mentioned spinel glass ceramics, comprises the following steps:
[0054] (1) Ingredients: weigh each raw material according to the formula, mix evenly, and obtain the ingredients;
[0055] (2) Melting: melting the batch material at 1650°C for 4 hours;
[0056] (3) Molding and annealing: pour the smelted molt...
PUM
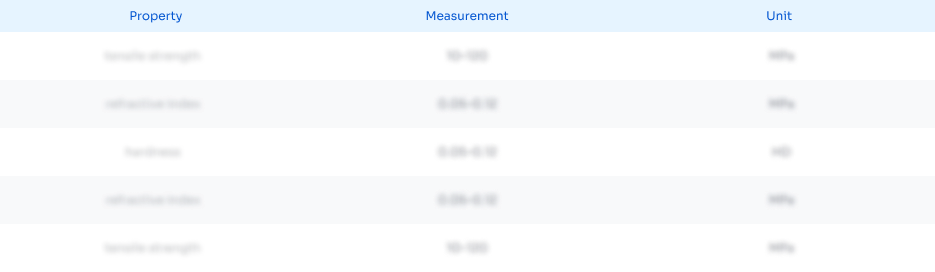
Abstract
Description
Claims
Application Information

- R&D
- Intellectual Property
- Life Sciences
- Materials
- Tech Scout
- Unparalleled Data Quality
- Higher Quality Content
- 60% Fewer Hallucinations
Browse by: Latest US Patents, China's latest patents, Technical Efficacy Thesaurus, Application Domain, Technology Topic, Popular Technical Reports.
© 2025 PatSnap. All rights reserved.Legal|Privacy policy|Modern Slavery Act Transparency Statement|Sitemap|About US| Contact US: help@patsnap.com