A kind of dyeing process of polyester fabric
A fabric and process technology, applied in the field of polyester fabric dyeing technology, can solve the problems of brittleness, yellowing of fabrics, and the unsatisfactory effect of fabric setting.
- Summary
- Abstract
- Description
- Claims
- Application Information
AI Technical Summary
Problems solved by technology
Method used
Image
Examples
Embodiment 1
[0054] refer to figure 1 , the dyeing process of a kind of polyester cloth disclosed by the invention, comprises the following steps:
[0055]S1: Gray cloth desizing; S2: Gray cloth pre-shrinking, soaking the gray cloth in clean water, and drying at 120-130°C; S3: Smoothing the finished cloth with a skin pass machine. Titanium dioxide hydrosol is added during the leveling process; S4: Pre-setting the flattened fabric. During the pre-setting process, the fabric is imported into the setting machine equipment for pre-setting treatment using a cloth loading machine. The pre-setting temperature is set at 185°C-190°C , the setting time is 45-60s; the first auxiliary agent is added in the process of putting on the cloth, and the first auxiliary agent includes the following components in parts by weight: 20 parts of sodium dodecylbenzenesulfonate; 3 parts of ammonium salt; 15 parts of sodium bicarbonate; 80 parts of water. S5: carry out alkali reduction treatment on the pre-set clot...
PUM
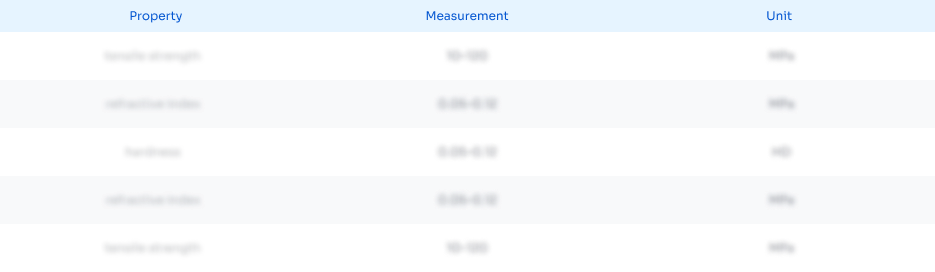
Abstract
Description
Claims
Application Information

- R&D
- Intellectual Property
- Life Sciences
- Materials
- Tech Scout
- Unparalleled Data Quality
- Higher Quality Content
- 60% Fewer Hallucinations
Browse by: Latest US Patents, China's latest patents, Technical Efficacy Thesaurus, Application Domain, Technology Topic, Popular Technical Reports.
© 2025 PatSnap. All rights reserved.Legal|Privacy policy|Modern Slavery Act Transparency Statement|Sitemap|About US| Contact US: help@patsnap.com