Racing tire tread rubber formula and preparation method thereof
A racing tire and surface rubber technology, which is applied in the field of racing tire tread rubber formula and its preparation, can solve the problems of difficult dispersion, high specific surface area carbon black filler mixing and heat generation, and difficulty in fully exerting the mechanics and mechanical properties of the formula. To achieve the effect of long mileage, long service life and excellent grip
- Summary
- Abstract
- Description
- Claims
- Application Information
AI Technical Summary
Problems solved by technology
Method used
Examples
Embodiment 1
[0019] Racing tread rubber formula, including by weight parts: 20 parts of natural rubber, 100 parts of styrene-butadiene rubber carbon black masterbatch, 30 parts of styrene-butadiene rubber, 5 parts of high styrene resin, 10 parts of carbon black BL101, 4 parts of aromatic oil 4 parts of rosin, 2 parts of anti-aging agent 4020, 1.5 parts of anti-aging agent RD, 5 parts of zinc oxide, 2 parts of stearic acid, 1.2 parts of sulfur, 1.5 parts of accelerator NS, and 0.4 parts of anti-scorch agent;
[0020] The preparation method of this racing car tread rubber comprises the steps:
[0021] (1) Master batch: the master batch adopts two-stage rubber mixing
[0022] One stage of masterbatch: in parts by weight, 20 parts of natural rubber, 100 parts of styrene-butadiene rubber carbon black masterbatch, 30 parts of styrene-butadiene rubber, 5 parts of high styrene resin, 10 parts of carbon black BL101, and 4 parts of aromatic oil , 4 parts of rosin, 1 part of anti-aging agent 4020, 1...
Embodiment 2
[0026] Racing tread rubber formula, including by weight parts: 10 parts of natural rubber, 110 parts of styrene-butadiene rubber carbon black masterbatch, 13 parts of styrene-butadiene rubber, 10 parts of high styrene resin, 25 parts of carbon black BL201, 8 parts of aromatic oil 2 parts of rosin, 2 parts of anti-aging agent 4020, 1.5 parts of anti-aging agent RD, 5 parts of zinc oxide, 2 parts of stearic acid, 1.6 parts of sulfur, 1 part of accelerator CZ, 0.3 part of anti-scorch agent;
[0027] The preparation method of this racing car tread rubber comprises the steps:
[0028] (1) Master batch: the master batch adopts two-stage rubber mixing
[0029] One stage of masterbatch: in parts by weight, 10 parts of natural rubber, 110 parts of styrene-butadiene rubber carbon black masterbatch, 13 parts of styrene-butadiene rubber, 10 parts of high styrene resin, 25 parts of carbon black BL201, and 8 parts of aromatic oil , 2 parts of rosin, 1.5 parts of anti-aging agent 4020, 1 pa...
Embodiment 3
[0033] Racing tread rubber formula, including by weight: 15 parts of natural rubber, 120 parts of styrene-butadiene rubber carbon black masterbatch, 5 parts of styrene-butadiene rubber, 3 parts of high styrene resin, 2 parts of carbon black BL101, 2 parts of carbon black BL201 3 parts, 5 parts of aromatic oil, 3 parts of rosin, 1.5 parts of anti-aging agent 4020, 1 part of anti-aging agent RD, 5 parts of zinc oxide, 2 parts of stearic acid, 0.9 parts of sulfur, 2 parts of accelerator NS, 0.1 part of anti-scorch agent ;
[0034] The preparation method of this racing car tread rubber comprises the steps:
[0035] One stage of masterbatch: in parts by weight, 15 parts of natural rubber, 120 parts of styrene-butadiene rubber carbon black masterbatch, 5 parts of styrene-butadiene rubber, 3 parts of high styrene resin, 2 parts of carbon black BL101, 3 parts of carbon black BL201 5 parts of aromatic oil, 3 parts of rosin, 1 part of anti-aging agent 4020, 1 part of anti-aging agent R...
PUM
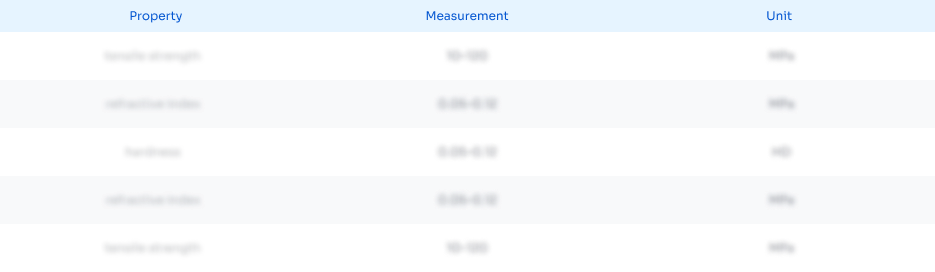
Abstract
Description
Claims
Application Information

- Generate Ideas
- Intellectual Property
- Life Sciences
- Materials
- Tech Scout
- Unparalleled Data Quality
- Higher Quality Content
- 60% Fewer Hallucinations
Browse by: Latest US Patents, China's latest patents, Technical Efficacy Thesaurus, Application Domain, Technology Topic, Popular Technical Reports.
© 2025 PatSnap. All rights reserved.Legal|Privacy policy|Modern Slavery Act Transparency Statement|Sitemap|About US| Contact US: help@patsnap.com