Emergency stop control method and system for robot
A control method and robot technology, applied in the field of robot control, can solve the problems of impact force evaluation without emergency stop, damage to the structure of the reducer, moving arm, and no reasonable interaction of the servo system, and achieve the effect of high cost performance and high integration.
- Summary
- Abstract
- Description
- Claims
- Application Information
AI Technical Summary
Problems solved by technology
Method used
Image
Examples
Embodiment 1
[0050] combined with figure 1 and figure 2As shown, an emergency stop control method for a robot, including:
[0051] A: The emergency stop switch of the external operation box (the safety emergency stop board can be connected to the emergency stop switch of the cabinet door, the emergency stop switch of the 4 external operation boxes and the teaching pendant) is used as a direct operating element, and the emergency stop switch adopts a double contact Normally closed contacts, the first pair of normally closed contacts is connected to the 24V terminal of the safety emergency stop board, and the second pair of normally closed contacts is connected to the GND of the safety emergency stop board. Terminal connected to the coil of the first safety relay of the safety emergency stop board and turned on; the double contact output of the emergency stop switch is output to the 24V end and GND end of the safety emergency stop board: the first safety relay is not connected when there i...
Embodiment 2
[0058] On the basis of Example 1, the emergency stop impulse time and deceleration parameters adopt the trapezoidal deceleration method to make the six axes decelerate and stop at the same time. The specific calculation method is:
[0059] (1) Calculate the emergency stop momentum time t dcc
[0060] Impulse time from emergency stop t dcc equal to the joint angular velocity divided by the joint angular acceleration get
[0061]
[0062] During the deceleration process, the joint torque τ of the reducer is less than or equal to the allowable torque value τ of acceleration and deceleration gdcc ,
[0063] get
[0064] τgdcc (2)
[0065] According to the Lagrangian dynamics formula, we get
[0066]
[0067] in, is the inertial force, is the centrifugal force and the Coriolis force, G(Θ) is the gravity part, M(Θ) is the moment of inertia matrix, is the relevant parts such as centrifugal force and Coriolis force, Θ is the joint angle, is the joint angular v...
Embodiment 3
[0078] combined with figure 1 And attached figure 2 As shown, a kind of emergency stop control system for the robot, including emergency stop switch, safety emergency stop board, drive and control integrated core, contactor and main power supply connected in sequence, also includes for the described safety emergency stop board and emergency stop switch power supply module, where:
[0079] The emergency stop switch includes a plurality of emergency stop buttons installed in the external operation box, and the emergency stop buttons are respectively connected to the safety emergency stop board;
[0080] The safety emergency stop board includes a first safety relay, a second safety relay and an ARM unit, and the first safety relay is respectively connected to the emergency stop switch and the drive-control integrated movement for receiving the emergency stop signal of the emergency stop switch and transmitted to the drive-control integrated core; the second safety relay is res...
PUM
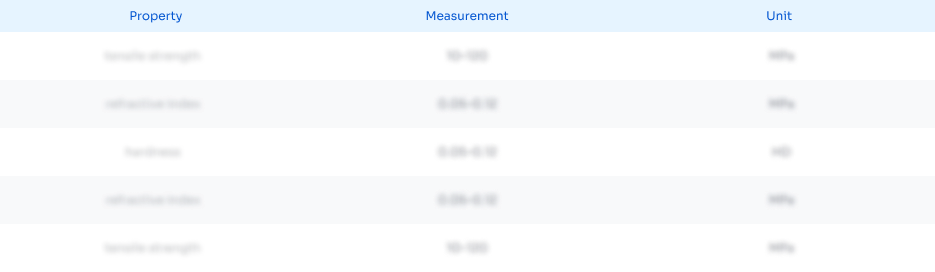
Abstract
Description
Claims
Application Information

- Generate Ideas
- Intellectual Property
- Life Sciences
- Materials
- Tech Scout
- Unparalleled Data Quality
- Higher Quality Content
- 60% Fewer Hallucinations
Browse by: Latest US Patents, China's latest patents, Technical Efficacy Thesaurus, Application Domain, Technology Topic, Popular Technical Reports.
© 2025 PatSnap. All rights reserved.Legal|Privacy policy|Modern Slavery Act Transparency Statement|Sitemap|About US| Contact US: help@patsnap.com