High-speed bar yield improvement method
A high-yield, high-line technology, applied in temperature control, metal rolling, etc., can solve the problems of reducing the rate of high-speed bar production, inconvenient use, and cumbersome steps, so as to reduce maintenance difficulty, ensure smooth production, The effect of reducing oxidation burning loss
- Summary
- Abstract
- Description
- Claims
- Application Information
AI Technical Summary
Problems solved by technology
Method used
Examples
Embodiment 1
[0026] A method for improving the high wire yield of rods, comprising the following steps:
[0027] 1) Improve the finished product rate by controlling the heating zone. The heating temperature is controlled at 1000°C, and the holding time after warming is 4 hours. The temperature at the beginning of heating in the heating furnace is 1100°C. 850℃, strictly implement the heating system, improve the heating efficiency, promote the uniform heating temperature of the billet, avoid black marks, reduce oxidation and burning loss, maintain normal furnace conditions, reduce the maintenance difficulty of the heating furnace bottom, and ensure smooth production;
[0028] 2) Adjust the roll gap of the finishing mill to reduce the occurrence of rolling scrap. It is necessary to ensure the accuracy of the roll gap of the finishing mill and the uniformity of each shift, to ensure that the head of the rolled piece in the finishing mill bites smoothly and the strip rolling state is good , the...
Embodiment 2
[0037] A method for improving the high wire yield of rods, comprising the following steps:
[0038] 1) Improve the finished product rate by controlling the heating zone. The heating temperature is controlled at 1200°C, and the holding time after heating is 5.5 hours. The temperature at the beginning of heating in the heating furnace is 1200°C. 900℃, strictly implement the heating system, improve the heating efficiency, promote the uniform heating temperature of the steel billet, avoid black marks, reduce oxidation and burning loss, maintain normal furnace conditions, reduce the maintenance difficulty of the heating furnace bottom, and ensure smooth production;
[0039] 2) Adjust the roll gap of the finishing mill to reduce the occurrence of rolling scrap. It is necessary to ensure the accuracy of the roll gap of the finishing mill and the uniformity of each shift, to ensure that the head of the rolled piece in the finishing mill bites smoothly and the strip rolling state is goo...
Embodiment 3
[0048] A method for improving the high wire yield of rods, comprising the following steps:
[0049] 1) Improve the finished product rate by controlling the heating zone. The heating temperature is controlled at 1400°C, and the holding time after heating is 7 hours. The temperature at the beginning of heating in the heating furnace is 1500°C. 1000℃, strictly implement the heating system, improve the heating efficiency, promote the uniform heating temperature of the steel billet, avoid black marks, reduce oxidation and burning loss, maintain normal furnace conditions, reduce the maintenance difficulty of the heating furnace bottom, and ensure smooth production;
[0050] 2) Adjust the roll gap of the finishing mill to reduce the occurrence of rolling scrap. It is necessary to ensure the accuracy of the roll gap of the finishing mill and the uniformity of each shift, to ensure that the head of the rolled piece in the finishing mill bites smoothly and the strip rolling state is good...
PUM
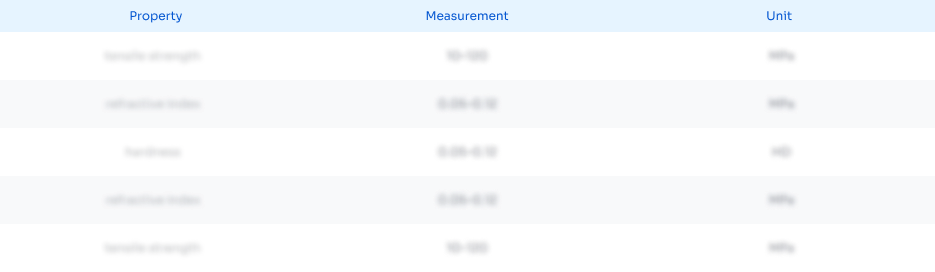
Abstract
Description
Claims
Application Information

- R&D
- Intellectual Property
- Life Sciences
- Materials
- Tech Scout
- Unparalleled Data Quality
- Higher Quality Content
- 60% Fewer Hallucinations
Browse by: Latest US Patents, China's latest patents, Technical Efficacy Thesaurus, Application Domain, Technology Topic, Popular Technical Reports.
© 2025 PatSnap. All rights reserved.Legal|Privacy policy|Modern Slavery Act Transparency Statement|Sitemap|About US| Contact US: help@patsnap.com