Remanufacturing method after scrapping of brazing tail thread
A remanufacturing and threading technology, applied in the field of shank manufacturing, can solve problems such as no repair technology, and achieve the effect of saving use costs
- Summary
- Abstract
- Description
- Claims
- Application Information
AI Technical Summary
Problems solved by technology
Method used
Image
Examples
Embodiment 1
[0046] T45-600 Sandvik HL700 rock drill tailpiece.
[0047] Check its material, 23CrNi3Mo (EN40B), male joint length 250mm, shank diameter 52mm, choose 23CrNi3Mo (EN40B), heat treatment method 1: carburizing at 930°C, then air cooling, carburizing layer thickness 0.8-1.0mm.
[0048] The remanufacturing process steps are:
[0049] a: Shot blasting is performed on the scrapped shanks to remove the rust on the surface;
[0050] b: overall non-destructive testing inspection;
[0051] c: Align with a 100 kN (10 ton) press in advance;
[0052] d: Cut off the damaged thread part, 230mm;
[0053] e: Use friction welding to weld the already-processed matching new threaded joint (fixed length 240mm);
[0054] f: After the welding place is annealed at 840°C, the inner and outer welding flashes, that is, welding nodules, are removed;
[0055] g: The welding place is quenched at 930°C again, and then air-cooled;
[0056] h: non-destructive testing of welds;
[0057] i: Straightening...
Embodiment 2
[0061] T45-700 Furukawa HD712 rock drill shank tail.
[0062] The customer requested that the length be longer, and the length was changed to 800mm. Check its material, 22SiMnCr2NiMo (FF710), male joint length 400mm, shank diameter 52mm, 25Cr3MnMo (SANBAR 23), heat treatment method 1: 930°C carburizing, then air cooling, carburizing layer thickness 0.6-0.8mm.
[0063] The remanufacturing process steps are:
[0064] a: Shot blasting is performed on the scrapped shanks to remove the rust on the surface;
[0065] b: overall non-destructive testing inspection;
[0066] c: Use a 100 kN (10-ton) press to straighten in advance;
[0067] d: Cut off the damaged thread part, 270mm;
[0068] e: Use friction welding technology to weld the already processed and matched new threaded joint (fixed length 380mm);
[0069] f: After the welding place is annealed at 840°C, the inner and outer welding flashes, that is, welding nodules, are removed;
[0070] g: The welding place is quenched a...
PUM
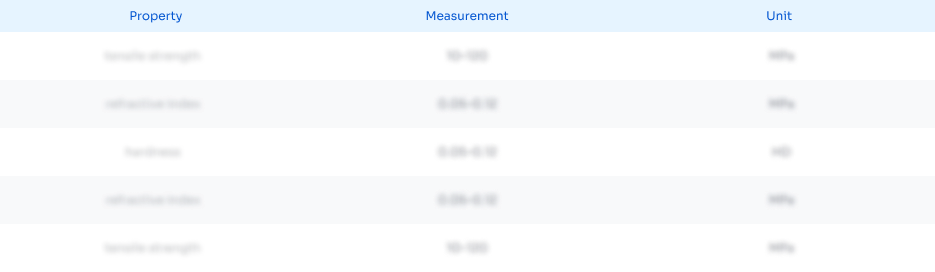
Abstract
Description
Claims
Application Information

- R&D
- Intellectual Property
- Life Sciences
- Materials
- Tech Scout
- Unparalleled Data Quality
- Higher Quality Content
- 60% Fewer Hallucinations
Browse by: Latest US Patents, China's latest patents, Technical Efficacy Thesaurus, Application Domain, Technology Topic, Popular Technical Reports.
© 2025 PatSnap. All rights reserved.Legal|Privacy policy|Modern Slavery Act Transparency Statement|Sitemap|About US| Contact US: help@patsnap.com