Preparation method of distributed Bragg reflector and vertical cavity surface emitting laser
A technology of Bragg reflector and refractive index layer, which is applied to lasers, laser components, semiconductor lasers, etc., can solve problems such as wafer warping, and achieve the effect of avoiding wafer warping and suppressing the occurrence of reverse domains
- Summary
- Abstract
- Description
- Claims
- Application Information
AI Technical Summary
Problems solved by technology
Method used
Image
Examples
preparation example Construction
[0039] The preparation method of the distributed Bragg reflector in the embodiment of the present invention is as follows,
[0040] S1. Provide substrate;
[0041] The substrate can be Ge or In 0.01 Ga 0.99 As, Al 0.57 Ga 0.43 As, Ga 0.5 In 0.5 One of P, the embodiment uses In 0.01 Ga 0.99 As an example;
[0042] S2. Alternate growth of N to Al x Ga 1-x As is the first refractive index layer of the material, Al y Ga 1-y As is the second refractive index layer of material.
[0043] The materials of the substrate, the first refractive index layer and the second refractive index layer of the present invention are not limited thereto, and can also be other materials, as long as the lattice constant of the substrate is guaranteed to be within the lattice constant of the first refractive index layer. and the lattice constant of the second refractive index layer.
[0044] The present invention adopts a substrate whose lattice constant is between the lattice constants of...
Embodiment 1
[0048] This embodiment provides a method for preparing a distributed Bragg reflector, taking x=0.90, y=0.15, and N=25, as follows:
[0049] (1) Determine the thickness of each layer:
[0050] Using ellipsometer to test the refractive index of the material at 940nm wavelength, Al 0.9 Ga 0.1 The refractive index of As is 3.028, Al 0.15 Ga 0.85 As is 3.466, use the formula d=λ / 4n to get Al 0.9 Ga 0.1 The thickness of As is 77.61nm, Al 0.15 Ga 0.85 The thickness of As is 67.80nm. The lattice constant of the substrate Ge is Al 0.9 Ga 0.1 As layer is Al 0.15 Ga 0.85 As layer is Nucleation layer Ga 0.50 In 0.50 P is In 0.01 Ga 0.99 As buffer layer is As, the stress compensation layer Ga 0.47 In 0.53 P is Using N×(77.62×0.002−67.8×0.004)+D×0.014+0.002×100−0.001×500=0, the thickness D of the strain compensation layer is 228.54 nm.
[0051] (2) Distributed Bragg reflectors grown on Ge substrates:
[0052] Sequential epitaxial growth of 100nm Ga from Ge sub...
Embodiment 2
[0056] This embodiment provides a method for preparing a distributed Bragg reflector, taking x=0.08, y=0.95, and N=35 as follows:
[0057] (1) Determine the thickness of the DBR layer and the thickness of the stress compensation layer:
[0058] Using ellipsometer to test the refractive index of the material at 940nm wavelength, Al x Ga 1-x The refractive index of As is 3.507, Al y Ga 1-y As is 2.999, use the formula d=λ / 4n to get Al x Ga 1-x The thickness of As is 67.02nm, Al y Ga 1-y The thickness of As is 78.36nm. Substrate In 0.01 Ga 0.99 The lattice constant of As is Al x Ga 1-x As layer is Al y Ga 1-y As layer In 0.01 Ga 0.99 As buffer layer is Stress compensation layer Ga 0.55 In 0.45 P is Using N×(78.36×0.004−67.02×0.003)−D×0.018=0, it can be known that the thickness D of the strain compensation layer is 218.52 nm.
[0059] (2) Growth In 0.01 Ga 0.99 Distributed Bragg reflectors on As substrates:
[0060] by In 0.01 Ga 0.99 Sequential ep...
PUM
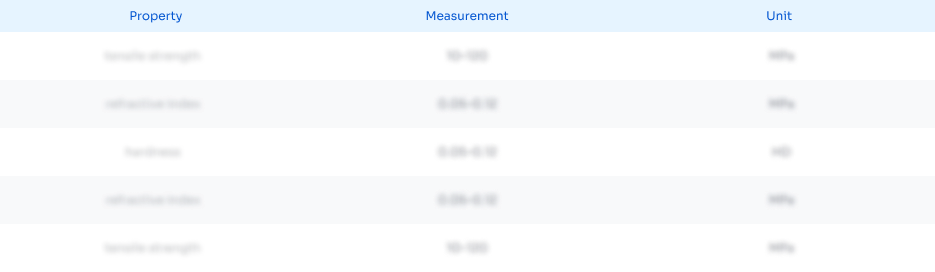
Abstract
Description
Claims
Application Information

- Generate Ideas
- Intellectual Property
- Life Sciences
- Materials
- Tech Scout
- Unparalleled Data Quality
- Higher Quality Content
- 60% Fewer Hallucinations
Browse by: Latest US Patents, China's latest patents, Technical Efficacy Thesaurus, Application Domain, Technology Topic, Popular Technical Reports.
© 2025 PatSnap. All rights reserved.Legal|Privacy policy|Modern Slavery Act Transparency Statement|Sitemap|About US| Contact US: help@patsnap.com