Liquid-liquid heterogeneous method for synthesizing polyarylether by utilizing continuous flow micro-channel reactor
A micro-channel reactor and channel reactor technology, applied in the field of liquid-liquid heterogeneous method
- Summary
- Abstract
- Description
- Claims
- Application Information
AI Technical Summary
Problems solved by technology
Method used
Image
Examples
Embodiment 1
[0029] Embodiment 1: as attached figure 1 , 2 and attached image 3 As shown, 0.37g CuBr, 5.24g N,N-di-n-butylamine, 1.51g pyridine and 0.036g trioctylmethylammonium chloride were dissolved in 100g toluene solution, followed by adding 80g 50wt% 2,6- The dimethylphenol / toluene solution was quickly stirred evenly to obtain the reaction solution A. The reaction solution A and 20wt% hydrogen peroxide were pumped into the straight channel module of the Corning high-throughput microchannel reactor through a metering pump for preheating. The preheating temperature was set to 35°C and the preheating residence time was 30s; The flux in the channel module is controlled at 4mL / min, the 2,6-dimethylphenol in the reaction solution A and the H in hydrogen peroxide 2 o 2 The molar ratio between them is 1:1.2. The preheated reaction solution A and 20wt% hydrogen peroxide were directly connected to the heart-shaped channel module of the Corning high-throughput microchannel reactor for mix...
Embodiment 2
[0030] Embodiment 2: as attached figure 1 , 2 and attached image 3 As shown, 0.38g CuBr, 5.32g N,N-di-n-butylamine, 1.50g pyridine and 0.051g trioctylmethylammonium chloride were dissolved in 100g toluene solution, followed by adding 80g 74wt% 2,3, 6-trimethylphenol / toluene solution and stirred rapidly to obtain reaction solution A. The reaction solution A and 30wt% hydrogen peroxide were pumped into the straight channel module of the Corning high-throughput microchannel reactor through the metering pump for preheating. The preheating temperature was set at 40°C and the preheating residence time was 30s; The flux in the channel module is controlled at 3.5mL / min, and the 2,3,6-trimethylphenol in the reaction solution A and the H in hydrogen peroxide 2 o 2 The molar ratio between them is 1:1.3. The preheated reaction solution A and 30wt% hydrogen peroxide were directly connected to the heart-shaped channel module of the Corning high-throughput microchannel reactor for mixe...
Embodiment 3
[0031] Embodiment 3: as attached figure 1 , 2 and attached image 3 As shown, 0.40g CuBr, 5.68g N,N-di-n-butylamine, 1.62g pyridine and 0.073g trioctylmethylammonium chloride were dissolved in 100g toluene solution, followed by adding 80g 78wt% 2,6- The dimethylphenol / toluene solution was quickly stirred evenly to obtain the reaction solution A. The reaction solution A and 30wt% hydrogen peroxide were pumped into the straight channel module of Corning high-throughput microchannel reactor through the metering pump for preheating. The preheating temperature was set at 45°C and the preheating residence time was 40s; The flux in the channel module is controlled at 3.5mL / min, the 2,6-dimethylphenol in the reaction solution A and the H in hydrogen peroxide 2 o 2 The molar ratio between them is 1:1.3. The preheated reaction solution A and 30wt% hydrogen peroxide were directly connected to the heart-shaped channel module of Corning high-throughput microchannel reactor for mixed r...
PUM
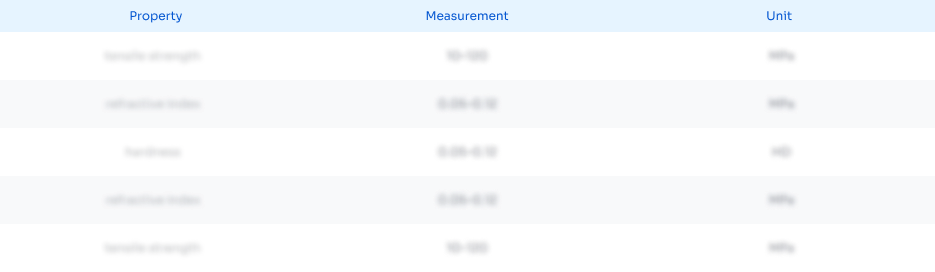
Abstract
Description
Claims
Application Information

- Generate Ideas
- Intellectual Property
- Life Sciences
- Materials
- Tech Scout
- Unparalleled Data Quality
- Higher Quality Content
- 60% Fewer Hallucinations
Browse by: Latest US Patents, China's latest patents, Technical Efficacy Thesaurus, Application Domain, Technology Topic, Popular Technical Reports.
© 2025 PatSnap. All rights reserved.Legal|Privacy policy|Modern Slavery Act Transparency Statement|Sitemap|About US| Contact US: help@patsnap.com