Re-welding repair method for ring weld joint of pipeline
A welding repair and girth weld technology, applied in welding equipment, welding accessories, tubular objects, etc., can solve the problems of unguaranteed welding quality and high welding work intensity, so as to reduce the intensity of manual operation, ensure welding quality, and ensure reliable Effect
- Summary
- Abstract
- Description
- Claims
- Application Information
AI Technical Summary
Problems solved by technology
Method used
Image
Examples
Embodiment 1
[0051]The in-service pipeline girth weld rewelding (surfacing) repair method provided by the present invention comprises the following steps:
[0052] 1) Clean up and clean the pipe girth weld 1 and adjacent areas;
[0053] 2) Conduct nondestructive testing on the pipeline girth weld 1 and adjacent areas to confirm that the pipeline girth weld 1 is suitable for repair by rewelding (surfacing);
[0054] 3) Arrange strain gauges near the girth weld 1 of the pipeline to monitor the stress and strain in the subsequent link. The steps are as follows: paste strain rosettes on both sides of the weld at points 3', 6', 9' and 12' of the pipeline , paste strain rosettes on alternate sides of the weld at points 1', 2', 4', 5', 7', 8', 10', and 11' of the pipeline. May be close to the original girth weld;
[0055] 4) If necessary, perform depressurization operation on pipeline 7 before pipeline girth welding repair (for example, reduce the pressure of natural gas pipeline 7 to below 80%...
Embodiment 2
[0074] Embodiment 2 is similar to Embodiment 1, with the difference that: between step 4.1) and step 4.2), the step of setting a separation layer is also included, and a welding separation layer 6 is installed on the repaired part of the girth weld to be re-welded. Such as image 3 and Figure 5 As shown, with the separation layer 6 as the basic mold layer, a shorter "B-type sleeve" is formed on the separation layer 6 by 3D printing (surfacing), so that the formed B-type sleeve bridges the original Both sides of the girth weld. When 3D printing (surfacing welding) is used to form a shorter size "B-type sleeve", the separation layer 6 will not melt the original girth weld, but the 3D printing (surfacing) "B-type sleeve" There is a certain gap between the inner wall and the original girth weld.
[0075] When the welding separation layer 6 is installed, the separation layer 6 is made of low-strength, high-plastic-tough material with a thickness of 1-2mm and a width of 20-25mm....
PUM
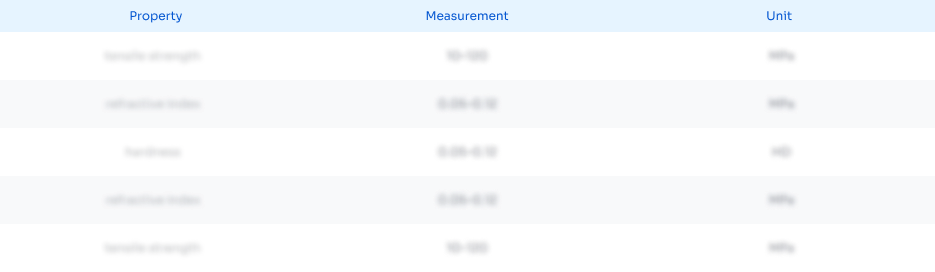
Abstract
Description
Claims
Application Information

- R&D
- Intellectual Property
- Life Sciences
- Materials
- Tech Scout
- Unparalleled Data Quality
- Higher Quality Content
- 60% Fewer Hallucinations
Browse by: Latest US Patents, China's latest patents, Technical Efficacy Thesaurus, Application Domain, Technology Topic, Popular Technical Reports.
© 2025 PatSnap. All rights reserved.Legal|Privacy policy|Modern Slavery Act Transparency Statement|Sitemap|About US| Contact US: help@patsnap.com